COUPLED TANKS GENERATION LABORATORY USER GUIDE
[ad_1]Introduction
Remote Laboratories
Remote laboratories enable students to access physical laboratory apparatus through the internet, providing a supplement to their studies and existing hands-on experience. Students carry out experiments using real equipment, but with much greater flexibility since access can occur from anywhere and at any time. Their interaction with the remote equipment is assisted by the use of data acquisition instrumentation and cameras, providing direct feedback to students for better engagement.
Traditional engineering laboratories require students to be physically present in order to work with equipment, which may limit student flexibility. Conversely, remote laboratories let students work in their own time and even repeat experiments for better learning outcomes.
Of course students cannot actually touch and feel the equipment in a remote laboratory, but they can still perform most other tasks relevant to their learning. Sometimes, separation from potentially hazardous equipment is preferable from a safety point of view.
Due to the increased use of remote operation in industry, where machinery and entire plants are often controlled from a distant location, students may directly benefit from learning how to remotely control equipment. Furthermore, remote laboratories provide the opportunity to access a wider range of experiments as costly or highly specialised equipment may not be locally available. This presents the opportunity to share laboratory facilities between institutions.
Significant research and pilot studies have been undertaken in Australia and by several groups around the world into the educational effectiveness of using remote laboratories. These studies have consistently shown that, if used appropriately in a way that is cognizant of the intended educational outcomes of the laboratory experience, remote laboratories can provide significant benefits.
Indeed, multiple research studies have demonstrated that whilst there are some learning outcomes that are achieved more effectively through hands-on experimentation (e.g. identification of assumptions, specific haptic skills), there are other learning outcomes that are achieved more effectively through remotely accessed laboratories (e.g. processing of data, understanding of concepts).
Engineering students are ab
le to access the Coupled Tanks Generation II v1 1 R igs to help them develop
and verify their mathematical models of the complex system dynamics involved in a SISO/MIMO coupled
tank system . The Coupled Tanks Generation II v1 1 allow s students to
Characteris e the behaviour of a Single Input Single Output (SISO) or Multi Input Multi Output (MIMO)
coupled tank system
Acquire experimental data to assist in developing a simplified model of the system.
Implement a PID controller to manage the inlet flow rate of water, such that the water level in th e
desired tank is kept constant.
Test a controller’s response to user initiated disturbances in the system.
Coupled Tanks Generation II v1-1 Laboratory User Guide
Version 2.3
University of Technology, Sydney © 2013 Page 3
1.2 Coupled Tanks Generation IICoupled Tanks Generation II — TheThe RigRig ApparatusApparatus
The Coupled Tanks Generation II
The Coupled Tanks Generation II v1v1–1 1 Rig Rig is a is a revision of the original Coupled Tanks Generation II Rig. The revision of the original Coupled Tanks Generation II Rig. The Rig was Rig was designed to allow students to designed to allow students to acquireacquire data from data from a physical dynamic system a physical dynamic system in order to developin order to develop a a simplified mathematical model of the underlying dynamics.simplified mathematical model of the underlying dynamics.
Once the mathematical models hav
Once the mathematical models have been developed, students are able to design a control system using a e been developed, students are able to design a control system using a P, PI, PD or PID controllerP, PI, PD or PID controller and analyse the performance of the controller in maintaining the water level in one and analyse the performance of the controller in maintaining the water level in one of the two tanksof the two tanks.. The rigs emulate a process engineering scenario wherebyThe rigs emulate a process engineering scenario whereby it may be critical to maintain a it may be critical to maintain a specific fluid level in a tank with single or multiple inputspecific fluid level in a tank with single or multiple input((ss)) and outputand output((ss)) acting upon the systemacting upon the system, allowing , allowing students to characterise the behaviour of such systems.students to characterise the behaviour of such systems.
Each Coupled Tanks Generation II Rig consists of the
Each Coupled Tanks Generation II Rig consists of the following main components:following main components:
1 x Frame
2 x Tanks
1 x Primary Tank
1 x Secondary Tank
1 x Reservoir
2 x Pumps
6 x Flow Meters
2 x Inlet Flow Meters
2 x Outlet Flow Meters
2 x Inter-Tank Flow Meters
2 x Control Valves
2 x Solenoid Valves
2 x Inter-Tank Coupling Valves
2 x Level Sensors with Magnetic Floats
Additionally, each Coupled Tanks Generation II Rig is monitored by a web camera
Additionally, each Coupled Tanks Generation II Rig is monitored by a web camera so as to provide so as to provide realreal–time time video of the system. The entire suite of Rigs is controlled by a Realvideo of the system. The entire suite of Rigs is controlled by a Real–Time I/O controller whicTime I/O controller which enables data h enables data acquisition and control of the components within each Rig. The control interface is written in LabVIEW.acquisition and control of the components within each Rig. The control interface is written in LabVIEW.
Figure Figure 11:: Coupled Tanks Generation II RigCoupled Tanks Generation II Rig v1v1–11..
Tank 1
Flow Meters
Tank 2
Reservoir
Level Sensors with Magnetic Floats
Control Valves
Inter-Tank Coupling Valves & Flow Meters
Coupled Tanks Generation II v1-1 Laboratory User Guide
Version 2.3
University of Technology, Sydney © 2013 Page 4
Using the Coupled Tanks RigUsing the Coupled Tanks Rig 2
There are two modes for using the Coupled Tanks Rigs, Manual Control and PID Control. This section
There are two modes for using the Coupled Tanks Rigs, Manual Control and PID Control. This section covers the basics of how to operate them. For covers the basics of how to operate them. For calibration datacalibration data on the various sensors, see the Rig on the various sensors, see the Rig Calibration document.Calibration document.
2.1 Manual ControlManual Control
Manual Control, also known as Open Loop Control, gives the user control over the inlet valve of the Coupled
Manual Control, also known as Open Loop Control, gives the user control over the inlet valve of the Coupled Tanks Rig. By varying the amount the valve is opeTanks Rig. By varying the amount the valve is open, users can manually regulate the amount of water n, users can manually regulate the amount of water entering Tank 1, and consequently Tank 2. This mode is useful for showing how difficult it can be for a human entering Tank 1, and consequently Tank 2. This mode is useful for showing how difficult it can be for a human to maintain a set point water level, as well as testing the rig’s functionality and allowing usto maintain a set point water level, as well as testing the rig’s functionality and allowing users to get used to ers to get used to the interface.the interface.
- Drag the slider to open/close the valve.
- Empty the tanks by clicking on the drain tab
- Watch the flow rates and tank levels rise on the graphs and diagram
Coupled Tanks Generation II v1-1 Laboratory User Guide
Version 2.3
University of Technology, Sydney © 2013 Page 5
2.2 PID ControlPID Control
PID Control, al
PID Control, also known as Closed Loop Control, allows the user to input variables (Kso known as Closed Loop Control, allows the user to input variables (Kpp, K, Kii, K, Kdd) and ) and implement a control loop feedback system. By adding the input variables and placing a setpoint water level, implement a control loop feedback system. By adding the input variables and placing a setpoint water level, the system will dynamically regulate tthe system will dynamically regulate the water flow into the Tank 1 to maintain the setpoint water level in he water flow into the Tank 1 to maintain the setpoint water level in Tank 2. Gaining understanding of the dynamics of such a control system is the primary aim of this Tank 2. Gaining understanding of the dynamics of such a control system is the primary aim of this experiment. experiment. - Switch to the PID tab. Enter control variables and water level setpoint, then press apply.
- Start data logging.
- Finish data logging, download the file and empty the tanks.
- Watch the graphs to see if the system behaves as desired.
Coupled Tanks Generation II v1-1 Laboratory User Guide
Version 2.3
University of Technology, Sydney © 2013 Page 6
Rig Control SoftwareRig Control Software 3
After being given access to the Coupled Tanks rig, you should see the
After being given access to the Coupled Tanks rig, you should see the following web interface:following web interface:
Figure
Figure 22:: Rig Control Software with the system operating in OpenRig Control Software with the system operating in Open–Loop Mode.Loop Mode.
This interface will provide you with both the controls for the Coupled Tanks as well as the data displays and
This interface will provide you with both the controls for the Coupled Tanks as well as the data displays and information you need to conduct your experiment. Most of the elements on the interface can be information you need to conduct your experiment. Most of the elements on the interface can be draggeddragged about, about, resizedresized, , minimisedminimised or or removedremoved based on your preferences. based on your preferences.
Coupled Tanks Diagram
Camera Element
Display Controls
Rig Controls
Data Logging Controls
Flow Rate Graph
Water Level Graph
Coupled Tanks Generation II v1-1 Laboratory User Guide
Version 2.3
University of Technology, Sydney © 2013 Page 7
3.1 Displays and LoggingDisplays and Logging ElementElement DescriptionDescription
A real time
A real time cameracamera feed of the Coupled Tanks feed of the Coupled Tanks rig. It shows the actual rig that is being operated rig. It shows the actual rig that is being operated by the interface. Tank 1 is on the left and Tank 2 by the interface. Tank 1 is on the left and Tank 2 is on the right.is on the right.
The camera
The camera streams in either Flash or Motion streams in either Flash or Motion Jpeg formats, both of which can be chosen on Jpeg formats, both of which can be chosen on the bottom right corner of the element.the bottom right corner of the element.
The Diagram element is an
The Diagram element is an representationrepresentation of the of the Coupled Tanks rig and incorporates the readouts Coupled Tanks rig and incorporates the readouts from the various sensors on the rigfrom the various sensors on the rig. .
It provides a quick visualisation of what is
It provides a quick visualisation of what is occurring at different parts of the rig in realoccurring at different parts of the rig in real–time, time, including including flow ratesflow rates, , water levelwater level, , valve valve percentagepercentage and and pump RPMpump RPM..
When using the Coupled Tanks, you will vary the
When using the Coupled Tanks, you will vary the opening of the opening of the valvevalve (valve percentage) to allow (valve percentage) to allow water to water to flowflow (flow rate) into the tanks and (flow rate) into the tanks and fillfill them (water level). The pump will always be them (water level). The pump will always be active.active.
This is the
This is the Display Control PanelDisplay Control Panel. It allows you . It allows you to close or open any element on the web to close or open any element on the web interface and to also reset theinterface and to also reset their positions on the ir positions on the web page.web page.
Remember, each element on the web interface
Remember, each element on the web interface can be moved about and resized.can be moved about and resized.
Coupled Tanks Generation II v1-1 Laboratory User Guide
Version 2.3
University of Technology, Sydney © 2013 Page 8
3.2 Rig Rig ControlsControls
The Coupled Tanks rig has two methods of control:
The Coupled Tanks rig has two methods of control: Manual (Open Loop) controlManual (Open Loop) control and and PID (Closed Loop)PID (Closed Loop) control. To switch between the two control. To switch between the two control modes, click the appropriate tab on the control element. control modes, click the appropriate tab on the control element.
Note:
Note: Switching between control modes disables the previous cSwitching between control modes disables the previous control and sets the valve to 0%ontrol and sets the valve to 0%
ElementElement DescriptionDescription
This tab shows the
This tab shows the Manual ControlManual Control or “Open or “Open Loop” control for the Coupled Tanks. Open Loop Loop” control for the Coupled Tanks. Open Loop control allows you to manually control the valve, control allows you to manually control the valve, allowing you to regulate the flow of water into the allowing you to regulate the flow of water into the tanks.tanks.
To set the valve percentage, you can either
To set the valve percentage, you can either drag drag the sliderthe slider horizontally or type a specifihorizontally or type a specific value in c value in the the input boxinput box..
This tab shows the
This tab shows the PID ControlPID Control or “Closed Loop” or “Closed Loop” control. Closed Loop control uses a transfer control. Closed Loop control uses a transfer function (with variables function (with variables KKpp, , KKii and and KKdd) to control ) to control a system to reach a setpoint, which for the a system to reach a setpoint, which for the Coupled Tanks is water level in the taCoupled Tanks is water level in the tanks.nks.
To set the variables or to choose a setpoint, type
To set the variables or to choose a setpoint, type your values into the appropriate input boxes and your values into the appropriate input boxes and presspress ApplyApply..
Select
Selecting this tab will result in the ing this tab will result in the drainingdraining of of both tanks. The solenoid valve at the bottom of both tanks. The solenoid valve at the bottom of Tank 1 will open, allowing for the tanks to quickly Tank 1 will open, allowing for the tanks to quickly drain, empty and reset the experiment.drain, empty and reset the experiment.
Coupled Tanks Generation II v1-1 Laboratory User Guide
Version 2.3
University of Technology, Sydney © 2013 Page 9
3.3 GraphsGraphs & Data Logging& Data Logging
The two graph elements of the web interface plot the two types of results of the experiment: Water flow rates
The two graph elements of the web interface plot the two types of results of the experiment: Water flow rates and the tank water levels. Each element can be and the tank water levels. Each element can be resizedresized to make the graphs larger and clearer to see. Each to make the graphs larger and clearer to see. Each plot plot can be toggled on off using the swican be toggled on off using the switch on the legend. Also, tch on the legend. Also, autoauto–scalingscaling can be toggled by clicking on can be toggled by clicking on the Controls switch and then enabling autothe Controls switch and then enabling auto–scaling.scaling. ElementElement DescriptionDescription
The The Flow RateFlow Ratess graph element displays one graph element displays one of the control variables of the experiment. The of the control variables of the experiment. The graph plots the flow rates at three different graph plots the flow rates at three different points on the rig:points on the rig:
The flow from the pump to Tank 1 (Pink)
The flow between Tank 1 and Tank 2 (Blue)
The flow from the bottom of Tank 2 into the reservoir (Orange)
These colours correspond to the direction
These colours correspond to the direction arrows on the Coupled Tanks diagram on the arrows on the Coupled Tanks diagram on the web page.web page.
The
The Tank LevelsTank Levels graph element displays the graph element displays the setpoint variables of the experiment. The setpoint variables of the experiment. The graph plograph plots the water level within the two ts the water level within the two tanks, as well as the desired setpoint when tanks, as well as the desired setpoint when using Closed Loop Control:using Closed Loop Control:
Tank 1 Water Level (Yellow)
Tank 2 Water Level (Red)
Setpoint Water Level (Purple)
Coupled Tanks Generation II v1-1 Laboratory User Guide
Version 2.3
University of Technology, Sydney © 2013 Page 10
ElementElement DescriptionDescription
This is the Data Logging Control panel. By
This is the Data Logging Control panel. By selecting your file format and then toggling to selecting your file format and then toggling to Logging switch, you can begin to capture the Logging switch, you can begin to capture the experiment data. experiment data. Once you untoggle the Once you untoggle the Logging Logging switch, the web switch, the web page will make the file available for you to page will make the file available for you to download.download. If you have been logging data for a If you have been logging data for a large period of time, this may take a few minutes large period of time, this may take a few minutes to process.to process.
If you misplace or forget to download/turn off the
If you misplace or forget to download/turn off the logging before finishing your session, you can logging before finishing your session, you can retrieve your data files from the retrieve your data files from the Data FilesData Files tab tab on the on the RigRig SelectionSelection screen of Remote Labs.screen of Remote Labs.
The file types available are:
The file types available are:
.csv.csv: Comma Seperated Values: Comma Seperated Values
.xls.xls: Excel 2003 format: Excel 2003 format
.xlsx.xlsx: Excel 2007 format: Excel 2007 format
All of which can be opened on the latest version
All of which can be opened on the latest version of Excel.of Excel.
Coupled Tanks Generation II v1-1 Laboratory User Guide
Version 2.3
University of Technology, Sydney © 2013 Page 11
3.4 Data Logging File ContentsData Logging File Contents
The data logs produced by the experiment can be downloaded as either .csv, .xls, or .xlsx and can be used
The data logs produced by the experiment can be downloaded as either .csv, .xls, or .xlsx and can be used opened in most spreadsheet programs. The data logs containopened in most spreadsheet programs. The data logs contain the following fieldsthe following fields of data:of data: HeadingHeading DescriptionDescription
Timestamp (s)
Timestamp (s)
The time the sample was
The time the sample was taken in seconds, starting taken in seconds, starting from when the Logging was activated. The Coupled from when the Logging was activated. The Coupled Tanks sensors sample at 10Hz.Tanks sensors sample at 10Hz.
Setpoint (mm)
Setpoint (mm)
The Setpoint water level value that was input into the
The Setpoint water level value that was input into the PID controller during this sample. 0 when in manual PID controller during this sample. 0 when in manual mode.mode.
Kp
Kp
The Kp value that
The Kp value that was input into the PID controller was input into the PID controller during this sample. 0 when in manual mode.during this sample. 0 when in manual mode.
Ki
Ki
The Ki value that was input into the PID controller
The Ki value that was input into the PID controller during this sample. 0 when in manual mode.during this sample. 0 when in manual mode.
Kd
Kd
The Kd value that was input into the PID controller
The Kd value that was input into the PID controller during this sample. 0 whduring this sample. 0 when in manual mode.en in manual mode.
Valve %
Valve %
The amount the valve is open (in percent), regulating
The amount the valve is open (in percent), regulating the water flow into tank 1 at the time of the sample. the water flow into tank 1 at the time of the sample. When in manual mode, this will be determined by the When in manual mode, this will be determined by the user manually. When in PID mode, the PID controller user manually. When in PID mode, the PID controller will determine will determine this value.this value.
Pump (RPM)
Pump (RPM)
The RPM of the pump that is pumping water into
The RPM of the pump that is pumping water into Tank 1. The value should remain somewhat Tank 1. The value should remain somewhat consistent. If there are any major variances, then the consistent. If there are any major variances, then the experiment should be repeated.experiment should be repeated.
Tank 1 Level (mm)
Tank 1 Level (mm)
The water level in Tank 1 at the time o
The water level in Tank 1 at the time of the sample.f the sample.
Tank 2 Level (mm)
Tank 2 Level (mm)
The water level in Tank 2 at the time of the sample.
The water level in Tank 2 at the time of the sample.
Flow 1 (L/min)
Flow 1 (L/min)
The flow rate of water into Tank 1 at the time of the
The flow rate of water into Tank 1 at the time of the sample.sample.
Flow 2 (L/min)
Flow 2 (L/min)
The flow rate of water from Tank 1 to Tank 2 at the
The flow rate of water from Tank 1 to Tank 2 at the time of the sample.time of the sample.
Flow 3 (L/min)
Flow 3 (L/min)
The flow rate of water out of Tank 2 at the time of the
The flow rate of water out of Tank 2 at the time of the sample.sample.
Coupled Tanks Generation II v1-1 Laboratory User Guide
Version 2.3
University of Technology, Sydney © 2013 Page 12
Rig SpecificationsRig Specifications 4
4.1 FrameFrame
The
The rrig ig fframe is made of Mayrame is made of MayTTec Aluminium Extrusion with a 40mm profile. The frame has a ec Aluminium Extrusion with a 40mm profile. The frame has a 6 6 mmmm thick thick aaluminium baseluminium base–plate plate to to support the reservoir support the reservoir andand the tanks. An additionalthe tanks. An additional circular cutcircular cut–out allowout allowss for access for access to the reservoir drto the reservoir drain plug ain plug duringduring system maintenance. The backsystem maintenance. The back–plate is plate is made from made from 66 mmmm thickthick aluminium aluminium and has been CNC machined with numerous chamfered throughand has been CNC machined with numerous chamfered through–holes for component wiring.holes for component wiring.
4.2 TanksTanks
The tanks are made of rigid PVC and clear PVC Schedule 40 pipe
The tanks are made of rigid PVC and clear PVC Schedule 40 pipe. . Each tank has a recess for the level Each tank has a recess for the level sensorsensor and a stepped outlet so as to compensate for the “deadand a stepped outlet so as to compensate for the “dead–zone” of zone” of the levelthe level sensor. sensor. Each tank has a Each tank has a CNC machined cutoutCNC machined cutout for a solenoid valve, allowing the user to quickly drain the system or alternate for a solenoid valve, allowing the user to quickly drain the system or alternate between Singlebetween Single–InputInput–SingleSingle–Output or MultiOutput or Multi–InputInput–MultiMulti–Output mode.Output mode. The tank also has an The tank also has an externalexternal overflow outlet overflow outlet to ensure that the water level does not to ensure that the water level does not exceed the design aexceed the design allowance of llowance of 330000 mmmm ((±± 2.52.5 mm)mm). . The tanks have a capacity of approximately The tanks have a capacity of approximately 22,,350350 cc (cc (22..3535 L) each.L) each.
4.3 ReservoirReservoir
The reservoir acts as a common water supply for the system, supplying both pumps and has a capacity of
The reservoir acts as a common water supply for the system, supplying both pumps and has a capacity of approximately approximately 2525,,0000 cc (00 cc (2525..00 L).L). The reservoThe reservoir has been designed such that even with both tanks ir has been designed such that even with both tanks operating at maximum level, sufficient water level (head) isoperating at maximum level, sufficient water level (head) is provided above the pump inlet to provided above the pump inlet to avoid the avoid the formation offormation of inlet vortinlet vorticesices and the consequential effects of airand the consequential effects of air–ingestion, such as cavitation.ingestion, such as cavitation.
4.4 PumpPumpss
The pumps are Swiftech MCP
The pumps are Swiftech MCP–35X branded units, which are 35X branded units, which are rere–badgedbadged Laing Thermotech Laing Thermotech DDCsDDCs utilising a utilising a DDC3.1DDC3.1–PWM PCB (PrintedPWM PCB (Printed–CircuitCircuit–Board)Board). The MCP. The MCP–35X 35X isis an electronically commutated spherical motor an electronically commutated spherical motor pumppump.. The only moving part in the The only moving part in the unitunit is the is the permanentpermanent–magnet magnet spherical spherical impellerimpeller and and this is supported by this is supported by aa ballball–shaped ceramic bearing.shaped ceramic bearing.
The implementation of such a bearing effectively eliminates bearing play and any associated noise
The implementation of such a bearing effectively eliminates bearing play and any associated noise increaseincrease and ensures thatand ensures that the bearing is selfthe bearing is self–realigning. The internal components are lubricated directly by realigning. The internal components are lubricated directly by the media being pumped (known as a wetthe media being pumped (known as a wet–rotor design). rotor design).
The permanent
The permanent–magnetic impeller is driven by a stator magnetic impeller is driven by a stator –– built into the pump housing built into the pump housing — that wraps a that wraps a magnetic field aromagnetic field around the impellerund the impeller, as this field is switched on and off, the impeller rotates, as this field is switched on and off, the impeller rotates. The MCP. The MCP–35X 35X features RPM (tachometer) output as well as PWM (Pulsefeatures RPM (tachometer) output as well as PWM (Pulse–WidthWidth–Modulation) speed controlModulation) speed control inputinput.. SSpecifications are given below:pecifications are given below: Pump SpecificationsPump Specifications
Manufacturer:
Manufacturer:
Swift
Swiftech / Laing Thermotechech / Laing Thermotech
Model Number:
Model Number:
MCP
MCP–35X / DDC3.135X / DDC3.1–PWM.PWM.
Motor type:
Motor type:
Electronically Commutated
Electronically Commutated, Brushless DC, Spherical Motor, Brushless DC, Spherical Motor
Bearing Type:
Bearing Type:
Spherical Ceramic Ball
Spherical Ceramic Ball
Operating RPM:
Operating RPM:
1,300
1,300 –– 4,500 (via PWM)4,500 (via PWM)
Operating Voltage Range:
Operating Voltage Range:
9
9 –– 13.4 VDC13.4 VDC
Nominal
Nominal Voltage:Voltage:
12 VDC
12 VDC
Max. Nominal Current Draw
Max. Nominal Current Draw @ 12 VDC@ 12 VDC::
1.5 A
1.5 A
Max. Nominal Power Draw
Max. Nominal Power Draw @ 12 VDC@ 12 VDC::
18 W
18 W
Max. Nominal Head
Max. Nominal Head @ 12 VDC@ 12 VDC::
4.4 mH
4.4 mH22OO
Max. Nominal Flow Rate
Max. Nominal Flow Rate @@ 1212 VDCVDC::
0.29
0.2922 L/s (17.5 L/s (17.5 L/minL/min))
RPM Signal:
RPM Signal:
Open Collector 20mA, 0
Open Collector 20mA, 0–24 VDC24 VDC Square WaveSquare Wave 2 2 pulses per revolutionpulses per revolution
PWM Signal:
PWM Signal:
5V DC, 20
5V DC, 20–25 kHz25 kHz
Fittings:
Fittings:
G¼”
G¼” BSPP Female Threaded Inlet & OutletBSPP Female Threaded Inlet & Outlet
Coupled Tanks Generation II v1-1 Laboratory User Guide
Version 2.3
University of Technology, Sydney © 2013 Page 13
4.5 Flow Flow MetersMeters
The flow
The flow metersmeters are Parker DataFlow Compact DFC9000100 units. are Parker DataFlow Compact DFC9000100 units. These are inThese are in–lineline impellerimpeller–type units type units that that output a pulse as the impeller output a pulse as the impeller revolves in the fluid flow.revolves in the fluid flow. They do this by shining an infraThey do this by shining an infra–red beam red beam perpendicular to the axis of rotation of the impellerperpendicular to the axis of rotation of the impeller through to a sensor, creating what is known as a photothrough to a sensor, creating what is known as a photo–interrupterinterrupter..
As the impeller spins, it interrupts the beam, creating a “pulse
As the impeller spins, it interrupts the beam, creating a “pulse” in the output voltage. The ” in the output voltage. The onon–board board circuitcircuitryry has been designed such that this output voltage is a square wavehas been designed such that this output voltage is a square wave. The manufacturer . The manufacturer providesprovides a typa typical “Kical “K–factor” for calibration that states how many pulses equate to a given flow rate.factor” for calibration that states how many pulses equate to a given flow rate. The units are equippedThe units are equipped with with G3/8” BSPP maleG3/8” BSPP male–threaded connectors and threaded connectors and havehave an internal diameter of approximately 10mm.an internal diameter of approximately 10mm. SSpecifications are given below:pecifications are given below: Flow Meter SpecificationsFlow Meter Specifications
Manufacturer:
Manufacturer:
Parker Hannifin
Parker Hannifin
Model Number:
Model Number:
DataFlow Compact DFC900010
DataFlow Compact DFC90001000
Flow Meter Type:
Flow Meter Type:
In
In–lineline,, impellerimpeller–typetype
Operating Voltage:
Operating Voltage:
5 VDC
5 VDC
Operating Range:
Operating Range:
1
1–25 L/min25 L/min
Pressure Drop:
Pressure Drop:
1 mH
1 mH22O @ 15 L/minO @ 15 L/min
K
K–Factor:Factor:
752 pulses per Litre (Typical)
752 pulses per Litre (Typical)
Accuracy:
Accuracy:
± 2% (Typical)
± 2% (Typical)
Repeatability:
Repeatability:
± 1%
± 1%
Output Signal:
Output Signal:
5V DC Square Wave
5V DC Square Wave
Fittings:
Fittings:
G3/8” BSPP Male
G3/8” BSPP Male Threaded Inlet & OutletThreaded Inlet & Outlet
For calibration data on the rig specific flow meters, please see the
For calibration data on the rig specific flow meters, please see the Rig CalibrationRig Calibration document.document.
Coupled Tanks Generation II v1-1 Laboratory User Guide
Version 2.3
University of Technology, Sydney © 2013 Page 14
4.6 Control ValvesControl Valves
The control valves are a hybrid unit, consisting of a Hass Manufacturing EPV
The control valves are a hybrid unit, consisting of a Hass Manufacturing EPV–375B Electronic Proportional 375B Electronic Proportional Valve and a Valve and a Leadshine Leadshine ND556ND556 Stepper Motor Controller.Stepper Motor Controller.
The EPV
The EPV–375B is a brass375B is a brass–bodied inbodied in–line globe valve with ½” NPT female threaded inlet & outlet. The valve line globe valve with ½” NPT female threaded inlet & outlet. The valve is actuated by a Moons 5618Sis actuated by a Moons 5618S–05D stepper motor05D stepper motor connected to the valve stem.connected to the valve stem. The The ND556ND556 is a is a high high performance performance stepper motor controllerstepper motor controller usingusing purepure–sinusoidal currentsinusoidal current control and allows a variety of settings control and allows a variety of settings such as motor current and microsuch as motor current and micro–step resolution to be programmed via DIP switchesstep resolution to be programmed via DIP switches. .
Specifications for this hybrid unit are given below:
Specifications for this hybrid unit are given below: Control Valve SpecificaControl Valve Specificationstions ValveValve
Manufacturer:
Manufacturer:
Hass Manufacturing
Hass Manufacturing
Model Number:
Model Number:
EPV
EPV–375B375B
Valve Type:
Valve Type:
In
In–line Globeline Globe
Material:
Material:
Brass
Brass
Flow Factor (K
Flow Factor (Kvv):):
1.47 (m
1.47 (m33/hr with /hr with ΔΔP 10 mHP 10 mH22O)O)
Actuation:
Actuation:
Moons 5618S
Moons 5618S–05D Stepper Motor05D Stepper Motor, , NEMA Size 23, 1.8° Full Step AngleNEMA Size 23, 1.8° Full Step Angle, 29, 29ΩΩ/Phase, /Phase, 0.42Nm0.42Nm
Fittings:
Fittings:
½” NPT Female Threaded Inlet & Outlet
½” NPT Female Threaded Inlet & Outlet ControlControl
Manufacturer:
Manufacturer:
Leadshine
Leadshine
Model Number:
Model Number:
ND556
ND556
Operating Voltage:
Operating Voltage:
24 VDC
24 VDC
Steps per Revolution:
Steps per Revolution:
800
800 (programmed)(programmed)
Motor Peak Current:
Motor Peak Current:
1.
1.44 A (programmed)A (programmed)
4.7 InterInter–Tank Coupling ValvesTank Coupling Valves
The tanks are coupled with a
The tanks are coupled with a pair of pair of fullway ball valves made by fullway ball valves made by Giacomo Cimberio S.P.AGiacomo Cimberio S.P.A. These valves . These valves have a G3/8” BSPhave a G3/8” BSPP female threaded inlet & outlet, Teflon stem and ball gaskets and a hot forged brass ball P female threaded inlet & outlet, Teflon stem and ball gaskets and a hot forged brass ball and body.and body.
To aid in maintenance of the system, UTS developed custom push
To aid in maintenance of the system, UTS developed custom push–fit connectors which attach the valves to fit connectors which attach the valves to the tanks. the tanks. The pushThe push–fit connectors use a double ofit connectors use a double o–ring system, which allows for easy removal of the ring system, which allows for easy removal of the coupling valves for maintenance, inspection & replacoupling valves for maintenance, inspection & replacement.cement. The specifications for the coupling valves are The specifications for the coupling valves are given below:given below: Coupling ValveCoupling Valve SpecificationSpecificationss
Manufacturer:
Manufacturer:
Giacomo Cimberio S.P.A
Giacomo Cimberio S.P.A
Model Number:
Model Number:
CIM31
CIM3122
Valve
Valve Type: Type:
Fullway Ball Valve, Butterfly Handle
Fullway Ball Valve, Butterfly Handle
Ball &
Ball & Body MaterialBody Material::
Hot Forged Brass
Hot Forged Brass
Stem &
Stem & Ball Gasket Material:Ball Gasket Material:
Teflon (P.T.F.E)
Teflon (P.T.F.E)
Flow Factor (K
Flow Factor (Kvv):):
10
10 (m(m33/hr with /hr with ΔΔP 10P 10 mHmH22OO))
Fittings:
Fittings:
G3/8” BSPP
G3/8” BSPP FemaleFemale Threaded Inlet & OutletThreaded Inlet & Outlet
Coupled Tanks Generation II v1-1 Laboratory User Guide
Version 2.3
University of Technology, Sydney © 2013 Page 15
4.8 Level Sensors with Magnetic FloatsLevel Sensors with Magnetic Floats
The level sensors used are MTS Temposonics GH Rod
The level sensors used are MTS Temposonics GH Rod–Style magnetostrictiveStyle magnetostrictive position sensors. These position sensors. These sensors use the principle of magnetostriction sensors use the principle of magnetostriction — a phenomena that causes a material to change shape a phenomena that causes a material to change shape during magnetisation. during magnetisation.
To allow the sensor to measure a level or distance,
To allow the sensor to measure a level or distance, an external magnet located at some position along the wave guide, generates its own magnetic field within that vicinity. The sensor sends a current pulse along the wave guide and when the current pulse reaches the position of the external magnet, the two magnetic fields interact, producing a strain pulse.
It is
It is the time between the current pulse and this returning strain pulse that is measured the time between the current pulse and this returning strain pulse that is measured by the sensor by the sensor and and then converted intothen converted into an output signal that corresponds with distance.an output signal that corresponds with distance.
The sensors used here output
The sensors used here output a 4a 4–20 mA current signal to the real time I/O controller, 20 mA current signal to the real time I/O controller, allowing forallowing for accurate accurate and and fastfast measurementmeasurements. To allow for measurement of the fluid levels. To allow for measurement of the fluid level in the couple tanks in the couple tanks –– a magnetic float is a magnetic float is used to provide the used to provide the requiredrequired external magnetic external magnetic field field to interact to interact with the current pulsewith the current pulse.. Specifications for the Specifications for the level sensors are provided below:level sensors are provided below: Level Sensor SpecificationsLevel Sensor Specifications
Manufacturer:
Manufacturer:
MTS
MTS
Model Number:
Model Number:
Temposonics GH Rod
Temposonics GH Rod–Style Magnetostrictive SensorStyle Magnetostrictive Sensor
Rod Material:
Rod Material:
304L Stainless Steel
304L Stainless Steel
Magnet
Magnet Type: Type:
Magnetic
Magnetic FloatFloat
Supply Voltage
Supply Voltage::
24 VDC
24 VDC
Update Time:
Update Time:
<1ms (Typical)
<1ms (Typical)
Resolution:
Resolution:
Infinite (Restricted by output ripple)
Infinite (Restricted by output ripple)
Non
Non–Linearity:Linearity:
<
< ±±0.02% Full Stroke (0.02% Full Stroke (±± 50 µm min.)50 μm min.)
Repeatability:
Repeatability:
<
< ±±0.001% Full Stroke (0.001% Full Stroke (±± 2.5 µm min.)2.5 μm min.)
Signal Output
Signal Output::
4
4–20 mA20 mA
Stroke:
Stroke:
300mm
300mm
Dead Zones:
Dead Zones:
51mm from Flat
51mm from Flat–Faced Flange, 63.5mm from Rod EndFaced Flange, 63.5mm from Rod End
For calibration data on the rig specific flow meters, please see the
For calibration data on the rig specific flow meters, please see the Rig CalibrationRig Calibration document.document.
Coupled Tanks Generation II v1-1 Laboratory User Guide
Version 2.3
University of Technology, Sydney © 2013 Page 16
4.9 Real Time I/O ControllerReal Time I/O Controller
The Coupled Tanks Generation II Rig is controlled by a National Instruments Compact Real
The Coupled Tanks Generation II Rig is controlled by a National Instruments Compact Real–Time I/O Time I/O Controller, aka cRIO. Controller, aka cRIO. The The cRIOcRIO chosen chosen — aa cRIOcRIO–9022 9022 — has has a 533MHz controller with 2GB storage, 256MB a 533MHz controller with 2GB storage, 256MB DDR2 RAM, USB/RS232 interfacesDDR2 RAM, USB/RS232 interfaces and dual Ethernet portsand dual Ethernet ports..
For I/O, the chassis
For I/O, the chassis — a cRIOa cRIO–9114 with embedded Xilinx Virtex9114 with embedded Xilinx Virtex–5 FPGA 5 FPGA — has 4x NI 9403 has 4x NI 9403 3232–Ch, 5 V/TTL, Ch, 5 V/TTL, 7μS Bidirectional Digital I/O Module7μS Bidirectional Digital I/O Modules installed as well as 1x NI 9208 s installed as well as 1x NI 9208 1616–Ch, ±20mA, 16Ch, ±20mA, 16–Bit, 200kS/s Bit, 200kS/s Current Input ModuleCurrent Input Module..
Interfacing to each rig is perf
Interfacing to each rig is performed via a custom PCB designed at UTS that reormed via a custom PCB designed at UTS that re–routes the I/O lines from the routes the I/O lines from the DB37 connector on each I/O module to a DB25 connector for each rig. This then simply connects via a DB37 connector on each I/O module to a DB25 connector for each rig. This then simply connects via a standard DB25 cable standard DB25 cable –– providing a complete and simplified I/O solution.providing a complete and simplified I/O solution. The useThe use of digital I/O and current of digital I/O and current (rather than voltage) based sensors reduces the amount of noise and signal degradation in the rig.(rather than voltage) based sensors reduces the amount of noise and signal degradation in the rig.
Control of the rig is performed through a LabVIEW application that communicates with the cRIO, presenting
Control of the rig is performed through a LabVIEW application that communicates with the cRIO, presenting the user with accuratethe user with accurate, real, real–time information and control of each rig.time information and control of each rig. Real Time I/O Controller SpecificationsReal Time I/O Controller Specifications
Manufacturer:
Manufacturer:
National Instruments (NI)
National Instruments (NI)
Controller:
Controller:
NI
NI cRIOcRIO–90229022 RealReal–Time I/O ControllerTime I/O Controller
Chassis:
Chassis:
NI
NI cRIOcRIO–91149114
Controller Specifications:
Controller Specifications:
533MHz controller with
533MHz controller with 2GB storage, 256MB DDR2 RAM2GB storage, 256MB DDR2 RAM
Chassis Specifications:
Chassis Specifications:
8
8–slot Virtexslot Virtex–5 LX 50 Reconfigurable Chassis5 LX 50 Reconfigurable Chassis
I/O Modules:
I/O Modules:
4 x NI 9403
4 x NI 9403 3232–Ch, 5 V/TTL, 7μS Bidirectional Digital I/O ModulesCh, 5 V/TTL, 7μS Bidirectional Digital I/O Modules 1 x NI 9208 1 x NI 9208 1616–Ch, ±20mA, 16Ch, ±20mA, 16–Bit, 200kS/s Current Input ModuleBit, 200kS/s Current Input Module
4.10 More More InformationInformation
A specification
A specification pack containing mpack containing more information on the hardware used ore information on the hardware used will be released at a later date as a will be released at a later date as a downloadable archive (.zip) file located on the session page downloadable archive (.zip) file located on the session page forfor each rigeach rig..
Coupled Tanks Generation II v1-1 Laboratory User Guide
Version 2.3
University of Technology, Sydney © 2013 Page 17
FAQ & TroubleshootingFAQ & Troubleshooting 5
5.1 Hardware LimitationsHardware Limitations
The following h
The following hardware limitations ardware limitations apply to the rigapply to the rig –– care should be taken to avoid mistaking real care should be taken to avoid mistaking real phenomena as faults and the limitations should be observed when selecting the operating parameters for phenomena as faults and the limitations should be observed when selecting the operating parameters for the rig. the rig.
5.1.1 Inlet Flow Rate / Pump Continuously On / Valve Minimum SettInlet Flow Rate / Pump Continuously On / Valve Minimum Settinging
You may notice that the pump can never be switched off and that water is always flowing into the tank,
You may notice that the pump can never be switched off and that water is always flowing into the tank, even when the valveeven when the valve positionposition is set at the minimum possible (0%). A design decision was made to avoid is set at the minimum possible (0%). A design decision was made to avoid startup lag of the pump complicating the experistartup lag of the pump complicating the experiment.ment.
As a result
As a result –– the pump is always on and its flow rate is modulated by the valve. In order to avoid the pump is always on and its flow rate is modulated by the valve. In order to avoid damaging the pump damaging the pump –– a minimum flow rate of approximately 1.0 L/min was deemed necessary a minimum flow rate of approximately 1.0 L/min was deemed necessary –– with this with this being achieved when the valve position is set at being achieved when the valve position is set at the minimum possible value of 0%.the minimum possible value of 0%.
5.1.2 Outlet Flow Meter & Low Water LevelOutlet Flow Meter & Low Water Level
T
The he outlet outlet flow meter flow meter readingsreadings for for each tankeach tank may may appear very highappear very high and/or may appear to change and/or may appear to change significantly significantly in in valuevalue when starting from the zerowhen starting from the zero–levellevel and whilst there is a low water level in the tankand whilst there is a low water level in the tank. . These readings These readings do not reflect the actual flow rate through the outletdo not reflect the actual flow rate through the outlet and and occuroccur as a result of the operating as a result of the operating principle of the flow metersprinciple of the flow meters in combination with design constraints of the systemin combination with design constraints of the system..
Above:
Above: FloFlow Meter Data Plot showing w Meter Data Plot showing inaccurate flow rate data due to air existing in the cavityinaccurate flow rate data due to air existing in the cavity.. Note the significant reading changes and sudden transition (~35s) to the true flow rateNote the significant reading changes and sudden transition (~35s) to the true flow rate..
When the
When the systemsystem operates from the initial zerooperates from the initial zero–level,level, air air exists in theexists in the tank outtank outletletss andand accordingly the accordingly the outlet flow meteroutlet flow meterss. This causes . This causes inaccurateinaccurate readingsreadings to be observedto be observed until such time that theuntil such time that the flow meter flow meter cavity cavity isis saturatedsaturated entirely with waterentirely with water –– as the flow meters operate on the principle photoas the flow meters operate on the principle photo–interruption via interruption via an impeller.an impeller.
Above:
Above: Section view of the tank base showing the integrated solenoid valve and flow meter positionSection view of the tank base showing the integrated solenoid valve and flow meter position..
Coupled Tanks Generation II v1-1 Laboratory User Guide
Version 2.3
University of Technology, Sydney © 2013 Page 18
5.1.1 Flow Meter SignalFlow Meter Signalss
The signals from the flow meters may appear to be quite noisy
The signals from the flow meters may appear to be quite noisy–– this is however not noise but an artefact this is however not noise but an artefact from the way the flow meters genfrom the way the flow meters generate their signal and can be viewed as a “quantisation” of the signal.erate their signal and can be viewed as a “quantisation” of the signal.
Above:
Above: Flow Meter Data Plot showing signal artefacts which may be mistaken for noiseFlow Meter Data Plot showing signal artefacts which may be mistaken for noise..
The units have a K
The units have a K–Factor of 752 pulses per litre. The data from the flow sensors is acquired byFactor of 752 pulses per litre. The data from the flow sensors is acquired by counting counting the number of pulses during the acquisition window. Currently the acquisition window is set to 2 Hz so as the number of pulses during the acquisition window. Currently the acquisition window is set to 2 Hz so as to allow a reasonable update frequency on the flow meter data plot.to allow a reasonable update frequency on the flow meter data plot.
When the flow rate is, for example, 1.0 Litre per minute (0.0167 L/s) on
When the flow rate is, for example, 1.0 Litre per minute (0.0167 L/s) one would expect 752 pulses per e would expect 752 pulses per minute (12.53 pulses per second). Since the acquisition window is 2 times per second (2 Hz), we would minute (12.53 pulses per second). Since the acquisition window is 2 times per second (2 Hz), we would expect to count 6.265 pulses.expect to count 6.265 pulses.
However, the flow meters generate their pulses through the use of a photo interrupter
However, the flow meters generate their pulses through the use of a photo interrupter –– an an eleelectromechanical method. Since we count the full number of pulses during the acquisition window ctromechanical method. Since we count the full number of pulses during the acquisition window (effectively rounding down to the nearest pulse each time) we would thus only count 6 pulses.(effectively rounding down to the nearest pulse each time) we would thus only count 6 pulses.
Small variations in the flow rate can thus have an effect on the dat
Small variations in the flow rate can thus have an effect on the data displayed. For 6 pulses, when the a displayed. For 6 pulses, when the value is converted into a flow rate using the Kvalue is converted into a flow rate using the K–Factor, we arrive at 0.957 L/min (0.0159 L/s), Factor, we arrive at 0.957 L/min (0.0159 L/s), approximately 4% lower than the true flow rate. Resolution at this flow rate is thus approximately 4% lower than the true flow rate. Resolution at this flow rate is thus ±± 20%.20%.
The good news is that as the flow rate increases, the error due to this rounding down becomes smaller. At
The good news is that as the flow rate increases, the error due to this rounding down becomes smaller. At 10 Litres per minute the error is only 1.1% of the true flow rate. Resolution at this flow rate is thus 10 Litres per minute the error is only 1.1% of the true flow rate. Resolution at this flow rate is thus ±± 2%.2%.
Above:
Above: Simplified Simplified diagramdiagram of how the flow meters generate their output signal.of how the flow meters generate their output signal.
1 Pulse
Fluid Flow
Impeller
Photo Interrupter
Coupled Tanks Generation II v1-1 Laboratory User Guide
Version 2.3
University of Technology, Sydney © 2013 Page 19
5.1.2 Overflow StateOverflow State
When the inlet flow rate to
When the inlet flow rate to Tank 1 and/or 2Tank 1 and/or 2 is set too highis set too high in Open Loop control modein Open Loop control mode, it is possible to , it is possible to reach an overflow statereach an overflow state..
The overflow state occurs when the inlet flow rate is significantly higher than the
The overflow state occurs when the inlet flow rate is significantly higher than the maximum maximum flow rate flow rate through the interthrough the inter–tank coupling valves.tank coupling valves.
As a result, the water level
As a result, the water level in in Tank 1 and/Tank 1 and/or 2or 2 reaches reaches aa maximum of approximately maximum of approximately 300300 mm mm ((±± 2.5 2.5 mmmm) ) and spills over into the overflowand spills over into the overflow tube attached to the tanktube attached to the tank..
When this occurs, the user will see a sudden transition to a continuous level on the level data plot and
When this occurs, the user will see a sudden transition to a continuous level on the level data plot and additionally the level readout fadditionally the level readout for or the overflowing tank(s)the overflowing tank(s) will show approximately will show approximately 300 mm.300 mm.
Above:
Above: Tank 1 reaching the overflow point of approximately Tank 1 reaching the overflow point of approximately 300300 mmmm, followed by Tank 2 soon after., followed by Tank 2 soon after.
It is important to note that once the tank
It is important to note that once the tank(s)(s) hahaveve reached reached the the overflowoverflow statestate, any data recorded for , any data recorded for certain certain modelling techniques modelling techniques –– e.g. e.g. step response step response — is invalid is invalid as the true level that would be reached cannot be as the true level that would be reached cannot be measuredmeasured..
Above:
Above: The interThe inter–tank flow rate (red) dropping as tank flow rate (red) dropping as the level in the level in Tank 2 Tank 2 attempts to match thatattempts to match that of Tank 1of Tank 1..
Coupled Tanks Generation II v1-1 Laboratory User Guide
Version 2.3
University of Technology, Sydney © 2013 Page 20
5.1.3 MMagnetic Float Bobbingagnetic Float Bobbing & Disturbance& Disturbance
When looking closely at the level sensor data for
When looking closely at the level sensor data for any tank being fed by a pumped inletany tank being fed by a pumped inlet –– it is possible to it is possible to see small fluctuations in the level.see small fluctuations in the level. There are two reasons for this There are two reasons for this –– the first is due to the way the water the first is due to the way the water flows into the tank and the second is due to the way the magnetic floats are coupled to the level sensors.flows into the tank and the second is due to the way the magnetic floats are coupled to the level sensors.
The water flow into the tanks is de
The water flow into the tanks is de–coupled except at the very upper reaches coupled except at the very upper reaches of the tank level (close to of the tank level (close to the overflow level of the overflow level of 300300 mm). This means that the flow stream exists in free air and reaches the water mm). This means that the flow stream exists in free air and reaches the water surface due to the effect of gravity.surface due to the effect of gravity.
When the flow stream hits the water surface, it thus
When the flow stream hits the water surface, it thus makesmakes a disturbance a disturbance –– creating smcreating small variations in the all variations in the water level recorded by the level sensors.water level recorded by the level sensors.
Additional variations in the water level are seen by the level sensors due to the magnetic floats having a
Additional variations in the water level are seen by the level sensors due to the magnetic floats having a significantly larger internal bore diameter when compared to the outer diameter of tsignificantly larger internal bore diameter when compared to the outer diameter of the level sensors. As a he level sensors. As a result, in a steady state condition result, in a steady state condition –– the floats move around with the water current in the tank.the floats move around with the water current in the tank.
These variations are very
These variations are very smallsmall (sub(sub–millimetre)millimetre) and should not impact any typical experiments and should not impact any typical experiments undertaken on the rigs.undertaken on the rigs.
Above:
Above: Small variationsSmall variations (white)(white) in the recorded water level due to surface disturbance and in the recorded water level due to surface disturbance and bobbing of the magnetic float. bobbing of the magnetic float.
Coupled Tanks Generation II v1-1 Laboratory User Guide
Version 2.3
University of Technology, Sydney © 2013 Page 21
5.2 Contacting SupportContacting Support
Any questions regarding the
Any questions regarding the nature of assessment tasks should initially be directed to the relevant nature of assessment tasks should initially be directed to the relevant academic. academic. If the If the user encounters any difficulties during the course of using the rigs, the “user encounters any difficulties during the course of using the rigs, the “Contact SupportContact Support” ” button should be used to request assbutton should be used to request assistance and report an incident.istance and report an incident.
The following popup will appear
The following popup will appear –– please please enter enter your name your name and a valid email addressand a valid email address, followed by , followed by a a category from thecategory from the “Type” drop down list.“Type” drop down list.
You may then enter a brief statement regarding
You may then enter a brief statement regarding the nature of the request in the nature of the request in the “Purpose” field. Be sure to the “Purpose” field. Be sure to enter as detailed a description as possible of the incident in the “Feedback” field.enter as detailed a description as possible of the incident in the “Feedback” field.
5.3 Providing FeedbacProviding Feedbackk
Users are strongly encouraged to leave feedback and comments of their experience with the rigs to help
Users are strongly encouraged to leave feedback and comments of their experience with the rigs to help improve the system, as well as any suggestions for additional features to be included in the future. improve the system, as well as any suggestions for additional features to be included in the future.
For
[Button id=”1″]
[ad_2]
Source link
"96% of our customers have reported a 90% and above score. You might want to place an order with us."
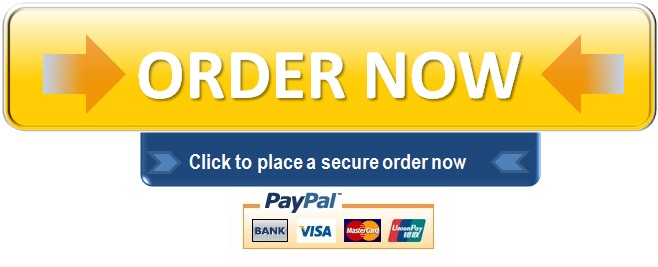