Tanks Generation II v1-1 Laboratory User Guide
[ad_1]
COUPLED TANKS GENERATION II RIG V1-1
LABORATORY USER GUIDE
VERSION 2.3
Partnered with… |
University of Technology, Sydney © 2013 |
Coupled Tanks Generation II v1-1 Laboratory User Guide
Version 2.3
University of Technology, Sydney © 2013 Page 1
Table of Contents
1 Introduction………………………………………………………………………………………………………………………………. 2
1.1 Remote Laboratories …………………………………………………………………………………………………………..2
1.2 Coupled Tanks Generation II – The Rig Apparatus …………………………………………………………………..3
2 Using the Coupled Tanks Rig ……………………………………………………………………………………………………… 4
2.1 Manual Control …………………………………………………………………………………………………………………..4
2.2 PID Control ………………………………………………………………………………………………………………………..5
3 Rig Control Software …………………………………………………………………………………………………………………. 6
3.1 Displays and Logging ………………………………………………………………………………………………………….7
3.2 Rig Controls ……………………………………………………………………………………………………………………….8
3.3 Graphs & Data Logging ……………………………………………………………………………………………………….9
4 Rig Specifications……………………………………………………………………………………………………………………. 12
4.1 Frame………………………………………………………………………………………………………………………………12
4.2 Tanks……………………………………………………………………………………………………………………………….12
4.3 Reservoir………………………………………………………………………………………………………………………….12
4.4 Pumps……………………………………………………………………………………………………………………………..12
4.5 Flow Meters ……………………………………………………………………………………………………………………..13
4.6 Control Valves…………………………………………………………………………………………………………………..13
4.7 Inter-Tank Coupling Valves …………………………………………………………………………………………………14
4.8 Level Sensors with Magnetic Floats …………………………………………………………………………………….15
4.9 Real Time I/O Controller …………………………………………………………………………………………………….16
4.10 More Information……………………………………………………………………………………………………………….16
5 FAQ & Troubleshooting ……………………………………………………………………………………………………………. 17
5.1 Hardware Limitations …………………………………………………………………………………………………………17
5.1.1 Inlet Flow Rate / Pump Continuously On / Valve Minimum Setting……………………………………… 17
5.1.2 Outlet Flow Meter & Low Water Level …………………………………………………………………………….. 17
5.1.1 Flow Meter Signals ………………………………………………………………………………………………………. 18
5.1.2 Overflow State …………………………………………………………………………………………………………….. 19
5.1.3 Magnetic Float Bobbing & Disturbance …………………………………………………………………………… 20
5.2 Contacting Support ……………………………………………………………………………………………………………21
5.3 Providing Feedback …………………………………………………………………………………………………………..21
Revision History
Rev | Date | Details | By |
2.0 | 20/03/2013 | Updated for v1-1 Rig Type | LJC |
2.1 | 25/03/2013 | Updated calibration data for Rig 3 | LJC |
2.2 | 27/03/2013 | Updated calibration data for Rig 4 | LJC |
2.3 | 8/8/2013 | Added “Using Coupled Tanks Rig” section. Updated the Rig Control Software section. Removed calibration data for Rigs. |
DA |
Coupled Tanks Generation II v1-1 Laboratory User Guide
Version 2.3
University of Technology, Sydney © 2013 Page 2
1 Introduction
1.1 Remote Laboratories
Remote laboratories enable students to access physical laboratory apparatus through the internet, providing
a supplement to their studies and existing hands-on experience. Students carry out experiments using real
equipment, but with much greater flexibility since access can occur from anywhere and at any time. Their
interaction with the remote equipment is assisted by the use of data acquisition instrumentation and
cameras, providing direct feedback to students for better engagement.
Traditional engineering laboratories require students to be physically present in order to work with
equipment, which may limit student flexibility. Conversely, remote laboratories let students work in their own
time and even repeat experiments for better learning outcomes.
Of course students cannot actually touch and feel the equipment in a remote laboratory, but they can still
perform most other tasks relevant to their learning. Sometimes, separation from potentially hazardous
equipment is preferable from a safety point of view.
Due to the increased use of remote operation in industry, where machinery and entire plants are often
controlled from a distant location, students may directly benefit from learning how to remotely control
equipment. Furthermore, remote laboratories provide the opportunity to access a wider range of experiments
as costly or highly specialised equipment may not be locally available. This presents the opportunity to share
laboratory facilities between institutions.
Significant research and pilot studies have been undertaken in Australia and by several groups around the
world into the educational effectiveness of using remote laboratories. These studies have consistently shown
that, if used appropriately in a way that is cognizant of the intended educational outcomes of the laboratory
experience, remote laboratories can provide significant benefits.
Indeed, multiple research studies have demonstrated that whilst there are some learning outcomes that are
achieved more effectively through hands-on experimentation (e.g. identification of assumptions, specific
haptic skills), there are other learning outcomes that are achieved more effectively through remotely
accessed laboratories (e.g. processing of data, understanding of concepts).
Engineering students are able to access the Coupled Tanks Generation II v1-1 Rigs to help them develop
and verify their mathematical models of the complex system dynamics involved in a SISO/MIMO coupled
tank system. The Coupled Tanks Generation II v1-1 allows students to:
| Characterise the behaviour of a Single Input Single Output (SISO) or Multi Input Multi Output (MIMO) coupled tank system. |
Acquire experimental data to assist in developing a simplified model of the system.
| Implement a PID controller to manage the inlet flow rate of water, such that the water level in the desired tank is kept constant. |
Test a controller’s response to user-initiated disturbances in the system.
Coupled Tanks Generation II v1-1 Laboratory User Guide
Version 2.3
University of Technology, Sydney © 2013 Page 3
1.2 Coupled Tanks Generation II – The Rig Apparatus
The Coupled Tanks Generation II v1-1 Rig is a revision of the original Coupled Tanks Generation II Rig. The
Rig was designed to allow students to acquire data from a physical dynamic system in order to develop a
simplified mathematical model of the underlying dynamics.
Once the mathematical models have been developed, students are able to design a control system using a
P, PI, PD or PID controller and analyse the performance of the controller in maintaining the water level in one
of the two tanks. The rigs emulate a process engineering scenario whereby it may be critical to maintain a
specific fluid level in a tank with single or multiple input(s) and output(s) acting upon the system, allowing
students to characterise the behaviour of such systems.
Each Coupled Tanks Generation II Rig consists of the following main components:
|
1 x Frame 2 x Tanks |
|
1 x Primary Tank 1 x Secondary Tank |
|
1 x Reservoir 2 x Pumps 6 x Flow Meters |
|
2 x Inlet Flow Meters 2 x Outlet Flow Meters 2 x Inter-Tank Flow Meters |
|
2 x Control Valves 2 x Solenoid Valves 2 x Inter-Tank Coupling Valves 2 x Level Sensors with Magnetic Floats |
Additionally, each Coupled Tanks Generation II Rig is monitored by a web camera so as to provide real-time
video of the system. The entire suite of Rigs is controlled by a Real-Time I/O controller which enables data
acquisition and control of the components within each Rig. The control interface is written in LabVIEW.
Figure 1: Coupled Tanks Generation II Rig v1-1.
Tank 1 Tank 2 |
Flow Meters
Reservoir
Level Sensors with
Magnetic Floats
Control Valves
Inter-Tank
Coupling Valves &
Flow Meters
Coupled Tanks Generation II v1-1 Laboratory User Guide
Version 2.3
University of Technology, Sydney © 2013 Page 4
2 Using the Coupled Tanks Rig
There are two modes for using the Coupled Tanks Rigs, Manual Control and PID Control. This section
covers the basics of how to operate them. For calibration data on the various sensors, see the Rig
Calibration document.
2.1 Manual Control
Manual Control, also known as Open Loop Control, gives the user control over the inlet valve of the Coupled
Tanks Rig. By varying the amount the valve is open, users can manually regulate the amount of water
entering Tank 1, and consequently Tank 2. This mode is useful for showing how difficult it can be for a human
to maintain a set point water level, as well as testing the rig’s functionality and allowing users to get used to
the interface.
1. Drag the slider to open/close
the valve.
3. Empty the tanks by clicking
on the drain tab
2. Watch the flow rates and
tank levels rise on the graphs
and diagram
Coupled Tanks Generation II v1-1 Laboratory User Guide
Version 2.3
University of Technology, Sydney © 2013 Page 5
2.2 PID Control
PID Control, also known as Closed Loop Control, allows the user to input variables (Kp, Ki, Kd) and
implement a control loop feedback system. By adding the input variables and placing a setpoint water level,
the system will dynamically regulate the water flow into the Tank 1 to maintain the setpoint water level in
Tank 2. Gaining understanding of the dynamics of such a control system is the primary aim of this
experiment.
2. Switch to the PID tab. Enter control variables and
1. Start data logging. water level setpoint, then press apply.
4. Finish data logging, download the file
and empty the tanks.
3. Watch the graphs to see
if the system behaves as
desired.
Coupled Tanks Generation II v1-1 Laboratory User Guide
Version 2.3
University of Technology, Sydney © 2013 Page 6
3 Rig Control Software
After being given access to the Coupled Tanks rig, you should see the following web interface:
Figure 2: Rig Control Software with the system operating in Open-Loop Mode.
This interface will provide you with both the controls for the Coupled Tanks as well as the data displays and
information you need to conduct your experiment. Most of the elements on the interface can be dragged
about, resized, minimised or removed based on your preferences.
Coupled Tanks
Diagram
Camera Element
Display Controls
Rig Controls
Data Logging
Controls
Flow Rate Graph Water Level
Graph
Coupled Tanks Generation II v1-1 Laboratory User Guide
Version 2.3
University of Technology, Sydney © 2013 Page 7
3.1 Displays and Logging
Element | Description |
A real time camera feed of the Coupled Tanks rig. It shows the actual rig that is being operated by the interface. Tank 1 is on the left and Tank 2 is on the right. The camera streams in either Flash or Motion Jpeg formats, both of which can be chosen on the bottom right corner of the element. |
|
The Diagram element is an representation of the Coupled Tanks rig and incorporates the readouts from the various sensors on the rig. It provides a quick visualisation of what is occurring at different parts of the rig in real-time, including flow rates, water level, valve percentage and pump RPM. When using the Coupled Tanks, you will vary the opening of the valve (valve percentage) to allow water to flow (flow rate) into the tanks and fill them (water level). The pump will always be active. |
|
This is the Display Control Panel. It allows you to close or open any element on the web interface and to also reset their positions on the web page. Remember, each element on the web interface can be moved about and resized. |
Coupled Tanks Generation II v1-1 Laboratory User Guide
Version 2.3
University of Technology, Sydney © 2013 Page 8
3.2 Rig Controls
The Coupled Tanks rig has two methods of control: Manual (Open Loop) control and PID (Closed Loop)
control. To switch between the two control modes, click the appropriate tab on the control element.
Note: Switching between control modes disables the previous control and sets the valve to 0%
Element | Description |
This tab shows the Manual Control or “Open Loop” control for the Coupled Tanks. Open Loop control allows you to manually control the valve, allowing you to regulate the flow of water into the tanks. To set the valve percentage, you can either drag the slider horizontally or type a specific value in the input box. |
|
This tab shows the PID Control or “Closed Loop” control. Closed Loop control uses a transfer function (with variables Kp, Ki and Kd) to control a system to reach a setpoint, which for the Coupled Tanks is water level in the tanks. To set the variables or to choose a setpoint, type your values into the appropriate input boxes and press Apply. |
|
Selecting this tab will result in the draining of both tanks. The solenoid valve at the bottom of Tank 1 will open, allowing for the tanks to quickly drain, empty and reset the experiment. |
Coupled Tanks Generation II v1-1 Laboratory User Guide
Version 2.3
University of Technology, Sydney © 2013 Page 9
3.3 Graphs & Data Logging
The two graph elements of the web interface plot the two types of results of the experiment: Water flow rates
and the tank water levels. Each element can be resized to make the graphs larger and clearer to see. Each
plot can be toggled on off using the switch on the legend. Also, auto-scaling can be toggled by clicking on
the Controls switch and then enabling auto-scaling.
Element | Description |
The Flow Rates graph element displays one of the control variables of the experiment. The graph plots the flow rates at three different points on the rig: The flow from the pump to Tank 1 (Pink) The flow between Tank 1 and Tank 2 (Blue) The flow from the bottom of Tank 2 into the reservoir (Orange) These colours correspond to the direction arrows on the Coupled Tanks diagram on the web page. |
|
The Tank Levels graph element displays the setpoint variables of the experiment. The graph plots the water level within the two tanks, as well as the desired setpoint when using Closed Loop Control: Tank 1 Water Level (Yellow) Tank 2 Water Level (Red) Setpoint Water Level (Purple) |
Coupled Tanks Generation II v1-1 Laboratory User Guide
Version 2.3
University of Technology, Sydney © 2013 Page 10
Element | Description |
This is the Data Logging Control panel. By selecting your file format and then toggling to Logging switch, you can begin to capture the experiment data. Once you untoggle the Logging switch, the web page will make the file available for you to download. If you have been logging data for a large period of time, this may take a few minutes to process. If you misplace or forget to download/turn off the logging before finishing your session, you can retrieve your data files from the Data Files tab on the Rig Selection screen of Remote Labs. The file types available are: .csv: Comma Seperated Values .xls: Excel 2003 format .xlsx: Excel 2007 format All of which can be opened on the latest version of Excel. |
Coupled Tanks Generation II v1-1 Laboratory User Guide
Version 2.3
University of Technology, Sydney © 2013 Page 11
3.4 Data Logging File Contents
The data logs produced by the experiment can be downloaded as either .csv, .xls, or .xlsx and can be used
opened in most spreadsheet programs. The data logs contain the following fields of data:
Heading | Description |
Timestamp (s) | The time the sample was taken in seconds, starting from when the Logging was activated. The Coupled Tanks sensors sample at 10Hz. |
Setpoint (mm) | The Setpoint water level value that was input into the PID controller during this sample. 0 when in manual mode. |
Kp | The Kp value that was input into the PID controller during this sample. 0 when in manual mode. |
Ki | The Ki value that was input into the PID controller during this sample. 0 when in manual mode. |
Kd | The Kd value that was input into the PID controller during this sample. 0 when in manual mode. |
Valve % | The amount the valve is open (in percent), regulating the water flow into tank 1 at the time of the sample. When in manual mode, this will be determined by the user manually. When in PID mode, the PID controller will determine this value. |
Pump (RPM) | The RPM of the pump that is pumping water into Tank 1. The value should remain somewhat consistent. If there are any major variances, then the experiment should be repeated. |
Tank 1 Level (mm) | The water level in Tank 1 at the time of the sample. |
Tank 2 Level (mm) | The water level in Tank 2 at the time of the sample. |
Flow 1 (L/min) | The flow rate of water into Tank 1 at the time of the sample. |
Flow 2 (L/min) | The flow rate of water from Tank 1 to Tank 2 at the time of the sample. |
Flow 3 (L/min) | The flow rate of water out of Tank 2 at the time of the sample. |
Coupled Tanks Generation II v1-1 Laboratory User Guide
Version 2.3
University of Technology, Sydney © 2013 Page 12
4 Rig Specifications
4.1 Frame
The rig frame is made of MayTec Aluminium Extrusion with a 40mm profile. The frame has a 6 mm thick
aluminium base-plate to support the reservoir and the tanks. An additional circular cut-out allows for access
to the reservoir drain plug during system maintenance. The back-plate is made from 6 mm thick aluminium
and has been CNC machined with numerous chamfered through-holes for component wiring.
4.2 Tanks
The tanks are made of rigid PVC and clear PVC Schedule 40 pipe. Each tank has a recess for the level
sensor and a stepped outlet so as to compensate for the “dead-zone” of the level sensor. Each tank has a
CNC machined cutout for a solenoid valve, allowing the user to quickly drain the system or alternate
between Single-Input-Single-Output or Multi-Input-Multi-Output mode. The tank also has an external
overflow outlet to ensure that the water level does not exceed the design allowance of 300 mm (± 2.5 mm).
The tanks have a capacity of approximately 2,350 cc (2.35 L) each.
4.3 Reservoir
The reservoir acts as a common water supply for the system, supplying both pumps and has a capacity of
approximately 25,000 cc (25.0 L). The reservoir has been designed such that even with both tanks
operating at maximum level, sufficient water level (head) is provided above the pump inlet to avoid the
formation of inlet vortices and the consequential effects of air-ingestion, such as cavitation.
4.4 Pumps
The pumps are Swiftech MCP-35X branded units, which are re-badged Laing Thermotech DDCs utilising a
DDC3.1-PWM PCB (Printed-Circuit-Board). The MCP-35X is an electronically commutated spherical motor
pump. The only moving part in the unit is the permanent-magnet spherical impeller and this is supported by
a ball-shaped ceramic bearing.
The implementation of such a bearing effectively eliminates bearing play and any associated noise
increase and ensures that the bearing is self-realigning. The internal components are lubricated directly by
the media being pumped (known as a wet-rotor design).
The permanent-magnetic impeller is driven by a stator – built into the pump housing – that wraps a
magnetic field around the impeller, as this field is switched on and off, the impeller rotates. The MCP-35X
features RPM (tachometer) output as well as PWM (Pulse-Width-Modulation) speed control input.
Specifications are given below:
Pump Specifications | |
Manufacturer: | Swiftech / Laing Thermotech |
Model Number: | MCP-35X / DDC3.1-PWM. |
Motor type: | Electronically Commutated, Brushless DC, Spherical Motor |
Bearing Type: | Spherical Ceramic Ball |
Operating RPM: | 1,300 – 4,500 (via PWM) |
Operating Voltage Range: | 9 – 13.4 VDC |
Nominal Voltage: | 12 VDC |
Max. Nominal Current Draw @ 12 VDC: | 1.5 A |
Max. Nominal Power Draw @ 12 VDC: | 18 W |
Max. Nominal Head @ 12 VDC: | 4.4 mH2O |
Max. Nominal Flow Rate @ 12 VDC: | 0.292 L/s (17.5 L/min) |
RPM Signal: | Open Collector 20mA, 0-24 VDC Square Wave 2 pulses per revolution |
PWM Signal: | 5V DC, 20-25 kHz |
Fittings: | G¼” BSPP Female Threaded Inlet & Outlet |
Coupled Tanks Generation II v1-1 Laboratory User Guide
Version 2.3
University of Technology, Sydney © 2013 Page 13
4.5 Flow Meters
The flow meters are Parker DataFlow Compact DFC9000100 units. These are in-line impeller-type units
that output a pulse as the impeller revolves in the fluid flow. They do this by shining an infra-red beam
perpendicular to the axis of rotation of the impeller through to a sensor, creating what is known as a photointerrupter.
As the impeller spins, it interrupts the beam, creating a “pulse” in the output voltage. The on-board circuitry
has been designed such that this output voltage is a square wave. The manufacturer provides a typical “Kfactor” for calibration that states how many pulses equate to a given flow rate. The units are equipped with
G3/8” BSPP male-threaded connectors and have an internal diameter of approximately 10mm.
Specifications are given below:
Flow Meter Specifications | |
Manufacturer: | Parker Hannifin |
Model Number: | DataFlow Compact DFC9000100 |
Flow Meter Type: | In-line, impeller-type |
Operating Voltage: | 5 VDC |
Operating Range: | 1-25 L/min |
Pressure Drop: | 1 mH2O @ 15 L/min |
K-Factor: | 752 pulses per Litre (Typical) |
Accuracy: | ± 2% (Typical) |
Repeatability: | ± 1% |
Output Signal: | 5V DC Square Wave |
Fittings: | G3/8” BSPP Male Threaded Inlet & Outlet |
For calibration data on the rig specific flow meters, please see the Rig Calibration document.
Coupled Tanks Generation II v1-1 Laboratory User Guide
Version 2.3
University of Technology, Sydney © 2013 Page 14
4.6 Control Valves
The control valves are a hybrid unit, consisting of a Hass Manufacturing EPV-375B Electronic Proportional
Valve and a Leadshine ND556 Stepper Motor Controller.
The EPV-375B is a brass-bodied in-line globe valve with ½” NPT female threaded inlet & outlet. The valve
is actuated by a Moons 5618S-05D stepper motor connected to the valve stem. The ND556 is a high
performance stepper motor controller using pure-sinusoidal current control and allows a variety of settings
such as motor current and micro-step resolution to be programmed via DIP switches.
Specifications for this hybrid unit are given below:
Control Valve Specifications | |
Valve | |
Manufacturer: | Hass Manufacturing |
Model Number: | EPV-375B |
Valve Type: | In-line Globe |
Material: | Brass |
Flow Factor (Kv): | 1.47 (m3/hr with ΔP 10 mH2O) |
Actuation: | Moons 5618S-05D Stepper Motor, NEMA Size 23, 1.8° Full Step Angle, 29Ω/Phase, 0.42Nm |
Fittings: | ½” NPT Female Threaded Inlet & Outlet |
Control | |
Manufacturer: | Leadshine |
Model Number: | ND556 |
Operating Voltage: | 24 VDC |
Steps per Revolution: | 800 (programmed) |
Motor Peak Current: | 1.4 A (programmed) |
4.7 Inter-Tank Coupling Valves
The tanks are coupled with a pair of fullway ball valves made by Giacomo Cimberio S.P.A. These valves
have a G3/8” BSPP female threaded inlet & outlet, Teflon stem and ball gaskets and a hot forged brass ball
and body.
To aid in maintenance of the system, UTS developed custom push-fit connectors which attach the valves to
the tanks. The push-fit connectors use a double o-ring system, which allows for easy removal of the
coupling valves for maintenance, inspection & replacement. The specifications for the coupling valves are
given below:
Coupling Valve Specifications | |
Manufacturer: | Giacomo Cimberio S.P.A |
Model Number: | CIM312 |
Valve Type: | Fullway Ball Valve, Butterfly Handle |
Ball & Body Material: | Hot Forged Brass |
Stem & Ball Gasket Material: | Teflon (P.T.F.E) |
Flow Factor (Kv): | 10 (m3/hr with ΔP 10 mH2O) |
Fittings: | G3/8” BSPP Female Threaded Inlet & Outlet |
Coupled Tanks Generation II v1-1 Laboratory User Guide
Version 2.3
University of Technology, Sydney © 2013 Page 15
4.8 Level Sensors with Magnetic Floats
The level sensors used are MTS Temposonics GH Rod-Style magnetostrictive position sensors. These
sensors use the principle of magnetostriction – a phenomena that causes a material to change shape
during magnetisation.
To allow the sensor to measure a level or distance, an external magnet located at some position along the
wave guide, generates its own magnetic field within that vicinity. The sensor sends a current pulse along
the wave guide and when the current pulse reaches the position of the external magnet, the two magnetic
fields interact, producing a strain pulse.
It is the time between the current pulse and this returning strain pulse that is measured by the sensor and
then converted into an output signal that corresponds with distance.
The sensors used here output a 4-20 mA current signal to the real time I/O controller, allowing for accurate
and fast measurements. To allow for measurement of the fluid level in the couple tanks – a magnetic float is
used to provide the required external magnetic field to interact with the current pulse. Specifications for the
level sensors are provided below:
Level Sensor Specifications | |
Manufacturer: | MTS |
Model Number: | Temposonics GH Rod-Style Magnetostrictive Sensor |
Rod Material: | 304L Stainless Steel |
Magnet Type: | Magnetic Float |
Supply Voltage: | 24 VDC |
Update Time: | <1ms (Typical) |
Resolution: | Infinite (Restricted by output ripple) |
Non-Linearity: | < ±0.02% Full Stroke (± 50 µm min.) |
Repeatability: | < ±0.001% Full Stroke (± 2.5 µm min.) |
Signal Output: | 4-20 mA |
Stroke: | 300mm |
Dead Zones: | 51mm from Flat-Faced Flange, 63.5mm from Rod End |
For calibration data on the rig specific flow meters, please see the Rig Calibration document.
Coupled Tanks Generation II v1-1 Laboratory User Guide
Version 2.3
University of Technology, Sydney © 2013 Page 16
4.9 Real Time I/O Controller
The Coupled Tanks Generation II Rig is controlled by a National Instruments Compact Real-Time I/O
Controller, aka cRIO. The cRIO chosen – a cRIO-9022 – has a 533MHz controller with 2GB storage, 256MB
DDR2 RAM, USB/RS232 interfaces and dual Ethernet ports.
For I/O, the chassis – a cRIO-9114 with embedded Xilinx Virtex-5 FPGA – has 4x NI 9403 32-Ch, 5 V/TTL,
7μS Bidirectional Digital I/O Modules installed as well as 1x NI 9208 16-Ch, ±20mA, 16-Bit, 200kS/s
Current Input Module.
Interfacing to each rig is performed via a custom PCB designed at UTS that re-routes the I/O lines from the
DB37 connector on each I/O module to a DB25 connector for each rig. This then simply connects via a
standard DB25 cable – providing a complete and simplified I/O solution. The use of digital I/O and current
(rather than voltage) based sensors reduces the amount of noise and signal degradation in the rig.
Control of the rig is performed through a LabVIEW application that communicates with the cRIO, presenting
the user with accurate, real-time information and control of each rig.
Real Time I/O Controller Specifications | |
Manufacturer: | National Instruments (NI) |
Controller: | NI cRIO-9022 Real-Time I/O Controller |
Chassis: | NI cRIO-9114 |
Controller Specifications: | 533MHz controller with 2GB storage, 256MB DDR2 RAM |
Chassis Specifications: | 8-slot Virtex-5 LX 50 Reconfigurable Chassis |
I/O Modules: | 4 x NI 9403 32-Ch, 5 V/TTL, 7μS Bidirectional Digital I/O Modules 1 x NI 9208 16-Ch, ±20mA, 16-Bit, 200kS/s Current Input Module |
4.10 More Information
A specification pack containing more information on the hardware used will be released at a later date as a
downloadable archive (.zip) file located on the session page for each rig.
Coupled Tanks Generation II v1-1 Laboratory User Guide
Version 2.3
University of Technology, Sydney © 2013 Page 17
5 FAQ & Troubleshooting
5.1 Hardware Limitations
The following hardware limitations apply to the rig – care should be taken to avoid mistaking real
phenomena as faults and the limitations should be observed when selecting the operating parameters for
the rig.
5.1.1 Inlet Flow Rate / Pump Continuously On / Valve Minimum Setting
You may notice that the pump can never be switched off and that water is always flowing into the tank,
even when the valve position is set at the minimum possible (0%). A design decision was made to avoid
startup lag of the pump complicating the experiment.
As a result – the pump is always on and its flow rate is modulated by the valve. In order to avoid
damaging the pump – a minimum flow rate of approximately 1.0 L/min was deemed necessary – with this
being achieved when the valve position is set at the minimum possible value of 0%.
5.1.2 Outlet Flow Meter & Low Water Level
The outlet flow meter readings for each tank may appear very high and/or may appear to change
significantly in value when starting from the zero-level and whilst there is a low water level in the tank.
These readings do not reflect the actual flow rate through the outlet and occur as a result of the operating
principle of the flow meters in combination with design constraints of the system.
Above: Flow Meter Data Plot showing inaccurate flow rate data due to air existing in the cavity.
Note the significant reading changes and sudden transition (~35s) to the true flow rate.
When the system operates from the initial zero-level, air exists in the tank outlets and accordingly the
outlet flow meters. This causes inaccurate readings to be observed until such time that the flow meter
cavity is saturated entirely with water – as the flow meters operate on the principle photo-interruption via
an impeller.
Above: Section view of the tank base showing the integrated solenoid valve and flow meter position.
Coupled Tanks Generation II v1-1 Laboratory User Guide
Version 2.3
University of Technology, Sydney © 2013 Page 18
5.1.1 Flow Meter Signals
The signals from the flow meters may appear to be quite noisy– this is however not noise but an artefact
from the way the flow meters generate their signal and can be viewed as a “quantisation” of the signal.
Above: Flow Meter Data Plot showing signal artefacts which may be mistaken for noise.
The units have a K-Factor of 752 pulses per litre. The data from the flow sensors is acquired by counting
the number of pulses during the acquisition window. Currently the acquisition window is set to 2 Hz so as
to allow a reasonable update frequency on the flow meter data plot.
When the flow rate is, for example, 1.0 Litre per minute (0.0167 L/s) one would expect 752 pulses per
minute (12.53 pulses per second). Since the acquisition window is 2 times per second (2 Hz), we would
expect to count 6.265 pulses.
However, the flow meters generate their pulses through the use of a photo interrupter – an
electromechanical method. Since we count the full number of pulses during the acquisition window
(effectively rounding down to the nearest pulse each time) we would thus only count 6 pulses.
Small variations in the flow rate can thus have an effect on the data displayed. For 6 pulses, when the
value is converted into a flow rate using the K-Factor, we arrive at 0.957 L/min (0.0159 L/s),
approximately 4% lower than the true flow rate. Resolution at this flow rate is thus ± 20%.
The good news is that as the flow rate increases, the error due to this rounding down becomes smaller. At
10 Litres per minute the error is only 1.1% of the true flow rate. Resolution at this flow rate is thus ± 2%.
Above: Simplified diagram of how the flow meters generate their output signal.
1 Pulse
Fluid
Flow
Impeller
Photo
Interrupter
Coupled Tanks Generation II v1-1 Laboratory User Guide
Version 2.3
University of Technology, Sydney © 2013 Page 19
5.1.2 Overflow State
When the inlet flow rate to Tank 1 and/or 2 is set too high in Open Loop control mode, it is possible to
reach an overflow state.
The overflow state occurs when the inlet flow rate is significantly higher than the maximum flow rate
through the inter-tank coupling valves.
As a result, the water level in Tank 1 and/or 2 reaches a maximum of approximately 300 mm (± 2.5 mm)
and spills over into the overflow tube attached to the tank.
When this occurs, the user will see a sudden transition to a continuous level on the level data plot and
additionally the level readout for the overflowing tank(s) will show approximately 300 mm.
Above: Tank 1 reaching the overflow point of approximately 300 mm, followed by Tank 2 soon after.
It is important to note that once the tank(s) have reached the overflow state, any data recorded for certain
modelling techniques – e.g. step response – is invalid as the true level that would be reached cannot be
measured.
Above: The inter-tank flow rate (red) dropping as the level in Tank 2 attempts to match that of Tank 1.
Coupled Tanks Generation II v1-1 Laboratory User Guide
Version 2.3
University of Technology, Sydney © 2013 Page 20
5.1.3 Magnetic Float Bobbing & Disturbance
When looking closely at the level sensor data for any tank being fed by a pumped inlet – it is possible to
see small fluctuations in the level. There are two reasons for this – the first is due to the way the water
flows into the tank and the second is due to the way the magnetic floats are coupled to the level sensors.
The water flow into the tanks is de-coupled except at the very upper reaches of the tank level (close to
the overflow level of 300 mm). This means that the flow stream exists in free air and reaches the water
surface due to the effect of gravity.
When the flow stream hits the water surface, it thus makes a disturbance – creating small variations in the
water level recorded by the level sensors.
Additional variations in the water level are seen by the level sensors due to the magnetic floats having a
significantly larger internal bore diameter when compared to the outer diameter of the level sensors. As a
result, in a steady state condition – the floats move around with the water current in the tank.
These variations are very small (sub-millimetre) and should not impact any typical experiments
undertaken on the rigs.
Above: Small variations (white) in the recorded water level due to surface disturbance and bobbing of the magnetic float.
Coupled Tanks Generation II v1-1 Laboratory User Guide
Version 2.3
University of Technology, Sydney © 2013 Page 21
5.2 Contacting Support
Any questions regarding the nature of assessment tasks should initially be directed to the relevant
academic. If the user encounters any difficulties during the course of using the rigs, the “Contact Support”
button should be used to request assistance and report an incident.
The following popup will appear – please enter your name and a valid email address, followed by a
category from the “Type” drop down list.
You may then enter a brief statement regarding the nature of the request in the “Purpose” field. Be sure to
enter as detailed a description as possible of the incident in the “Feedback” field.
5.3 Providing Feedback
Users are strongly encouraged to leave feedback and comments of their experience with the rigs to help
improve the system, as well as any suggestions for additional features to be included in the future.
For any enquires or assistance, contact the Labshare helpdesk at:
helpdesk@labshare.edu.au
[Button id=”1″]
[ad_2]
Source link
"96% of our customers have reported a 90% and above score. You might want to place an order with us."
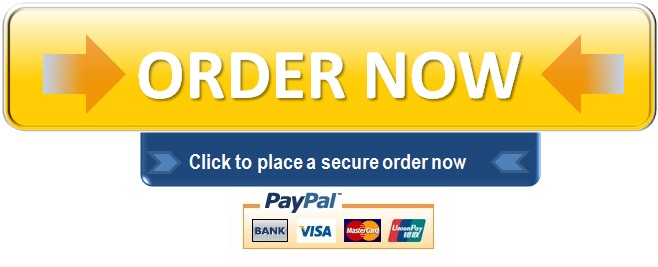