Assignment 3
Assignment 3: Interval Determination and Compiling of the Program Context
A key activity within the process of developing a maintenance program is the determination of intervention intervals. Mostly these are determined in practice by ‘experience’ or ‘engineering judgment’. The logic used for such practice is not normally explicit. It is important to make this logic accessible and to consider how to use available data to inform these decisions. Reliability data and cost information is sometimes available. Decision models utilizing such data have been established. It is important that you are aware, but not in awe, of these approaches to interval determination so that you can migrate your decision making to a more logical framework. The models are typically applicable to mechanical and electrical systems but may also have some application in more general systems and components.
Key Questions
- Which decision model adequately replicates the maintenance interval decision that needs to be made consistent with the available data?
- What use can be made of the available failure and cost data in order to make a more informed decision on a particular maintenance interval?
- How should the results of a particular decision model be interpreted and what decision should be made given this information and other information available?
- How can a practical interval be arrived at given the various constraints on cost, access, and synergies between required tasks?
Associated subject learning outcomes
The subject learning outcomes that are relevant to this assignment include:
- Demonstrate an understanding of the available theory in the area of maintenance requirements analysis.
- Apply appropriate theory to the problem of maintenance requirements analysis.
- Demonstrate an understanding of basic reliability theory and terminology.
- Design appropriate methods for performing maintenance requirements analysis on specific equipment given a specific situation.
Relevant topics Topic
1 – Preventive Maintenance and MRA Overview
Topic 3 – Determining relevant failure modes and their characteristics
Topic 4 – Task Determination Decision Logic
Topic 5 – Condition Based Renewal Tasks
Topic 6 – Usage Based Renewal Tasks
Topic 7 – Compiling Activities into a Program
Background:
A can-manufacturing line contains a number of systems that progressively manufacture cans from coated metal strip. The cans are then delivered to canning lines that fill them with food products: beans; tomatoes; pet food, for example. The can-manufacturing line utilises 6 interconnected rotating arm-assemblies that direct the cans to different operations. These arm-assemblies comprise the arm itself and a shaft supported in 2 bearings. The maintenance program for these arm-assemblies are under review as there is concern that the current program is not as good as it could be. You have been asked to provide advice. The current preventive maintenance program involves the replacement of each of the arm-assemblies (assemblies) during the annual shutdown. Where an assembly fails during the production period then it must be replaced to allow the production to continue.
Some considerable effort has been taken to understand the failure behaviour of these assemblies as their replacement is a major driver of the need for the annual shutdown. Analysis of past failures together with detailed assessment of the remaining lives of those assemblies removed at the annual shutdown have allowed reliability models to be estimated. The indications are that the shape parameter is 3.1, scale parameter 260 days and location parameter 220 days.
The arm assemblies are interconnected and housed together within the main frame of the machine. As a result, it takes 1.5 hours to gain access to the arm-assemblies and then a further 10 minutes to change each individual assembly. Following this it takes a further 2.5 hours to synchronise the arms and to adjust and restart the line
. Overhauling of an assembly costs $1600. The cost of replacing them under a planned situation, during a shutdown has been estimated to be $3600 per hour. This includes labour and lost production. Where the assembly must be replaced on failure, during scheduled production, then this cost involves a penalty of an additional $9500.
4 different options for a preventive maintenance program have been identified: (a) Continue with the current program; (b) Replacement of assemblies once they reach a pre-defined age; (c) replacement of the 6 assemblies as a replaceable unit at a regular shutdown or on failure; or, (d) replacement of the 6 assemblies on the failure of 1 assembly.
Tasks:
- ) Interpret each of the 4 options proposed to identify a relevant renewal model in each case and the specific parameters for each model, explaining your reasoning for each of these interpretations. (32 marks)
- ) Using quantitative analysis, compare the 4 options and recommend which of them is preferred. Suggest alternatives if appropriate and substantiate your suggestions. Justify your selection and identify any practical issues involved. (38 Marks)
- )Condition monitoring of the assemblies is being investigated. This involves the permanent installation of acoustic bearing devices on each assembly and connecting these to a remote test point to allow inspection during operation. The cost of inspection would be $180 and the likelihood of successful detection of incipient failure has been estimated as 0.85, based on experience with similar installations. Deterioration in condition is expected to be evident within 15 and 60 days before failure. An estimate of the resulting warning-time distribution results in a Weibull distribution with parameters: shape parameter 3.1, scale parameter 28 days and location parameter 14 days. What annual saving would this new option achieve in comparison to the preventive maintenance program that you identified in (ii)? (20 Marks)
iv.) An extension of the option set out in (iii) involves the continuous remote monitoring of the acoustic bearing devices. This option is believed would achieve 98% likelihood of successful detection of incipient failure with no additional inspection costs. What annual saving would this option achieve again in comparison to the program that you identified in (ii)? What would you need to consider in selecting this option? (10 Marks)
[Button id=”1″]
[ad_2]
Source link
"96% of our customers have reported a 90% and above score. You might want to place an order with us."
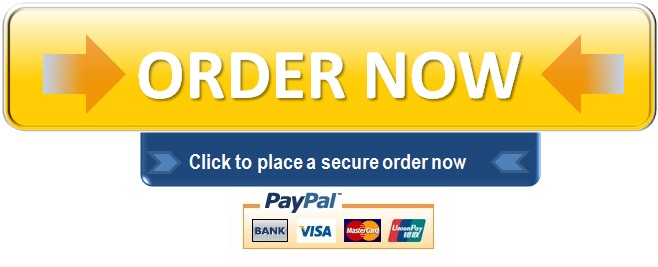