Complete a four-part assessment in which you will prepare a production cost report,
-
0
Assessment 3: Using Cost Accounting Concepts To Operate Job, Process, And Activity-Based Cost Systems
jess22
Complete a four-part assessment in which you will prepare a production cost report, allocate overhead using estimated costs and cost drivers, use cost analysis in the decision-making process, and compare the results of cost allocation processes.
Introduction
In the operation of a process cost accounting system, many manufacturing companies will uniformly apply materials, labor, and overhead, throughout the production process period. This is not necessarily true for other product and service companies whose production process requires adding materials at different points in the process. For these companies, cost calculation for each department in the production process is slightly more complex.
In some industries that use a manufacturing process operation, some units will always be lost due to shrinkage, spillage, or defects. These normal losses are expected as a necessary cost of producing high-quality products. They must be accounted for in the cost-of-production summary report. It is also possible—particularly when the process involves a liquid product— that units will be gained during production. This situation must also be accounted for and summarized in the production summary report.
Before beginning this assessment, take time to review the following topics:
Production cost report.
Activity-based costing.
Predetermined overhead allocation rates.
Quality improvement.
Allocation of service department costs.
Complete a four-part assessment in which you prepare a production cost report, allocate overhead using estimated costs and cost drivers, use cost analysis in the decision-making process, and compare the results of cost allocation processes.
Preparation
Use the Assessment 3 Template [XLSX] to complete the following four parts. Each part is a different tab in the template.
Part 1: In the template, prepare a production cost report using the FIFO method. Show all calculations and explain briefly.
Part 2: Compute overhead rate for each cost driver and production costs for each product, and compare to the consultant’s recommendations for cost drivers to explain the discrepancy between the two different approaches to product costing to management. Show all calculations.
Part 3: Compute and explain the rationale for using or not using the proposed new material based on the associated costs. Give other factors that should also be taken into consideration for this decision. Show all calculations.
Part 4: Allocate the cost to the service department using all three methods: direct, step, and reciprocal. Then comment on your findings in a paragraph. Show all calculations.
Instructions
Assessment 3 Part 1: Prepare a Production Cost Report: FIFO Method
In the template, prepare a production cost report using the FIFO method. Show all calculations and explain briefly.
Part 1 Scenario
Lamar, Inc. provides the following information for one of its department’s operations for May (no new material is added in Department T):
Lamar, Inc.: WIP Inventory: Department T
Item
Value
Beginning Inventory (16,500 units, 60% complete with respect to Department T costs)
Transferred-in Costs (from Department S)
$127,600
Department T Conversion Costs
$58,465
Current Work (38,500 units started)
Prior Department Costs
$308,000
Department T Costs
$229,955
Complete the following:
Prepare a production cost report using the FIFO method. Include an introduction.
Assessment 3 Part 2: Activity-Based Costing and Predetermined Overhead Allocation Rates
Compute overhead rate for each cost driver, production costs for each product, and compare to the consultant’s recommendations for cost drivers to explain the discrepancy between the two product costing approaches to management. Show all calculations.
Part 2 Scenario
Bath Fixtures Supply, Inc. (BFSI), manufactures three types of fixtures: industrial, standard, and brass. It applies all indirect costs according to a predetermined rate based on direct labor-hours. A consultant recently suggested that the company switch to an activity-based costing system and prepared the following cost estimates for year two for the recommended cost drivers.
BFSI: Costing System
Activity
Recommended Cost Driver
Estimated Cost
Estimated Cost Driver Activity
Order Processing
Number of orders
$59,400
200 orders
Production Setup
Number of production runs
$237,600
100 runs
Materials Handling
Pounds of materials used
$396,000
132,000 pounds
Machine Depreciation and Maintenance
Machine-hours
$316,800
13,200 hours
Quality Control
Number of inspections
$79,200
45 inspections
Packing
Number of units
$158,400
480,000 units
Total Estimated Cost
$1,247,400
In addition, management estimated 7,500 direct labor-hours for year two.
Assume that the following cost driver volumes occurred in January, year two:
BFSI: Cost Driver Volumes
Industrial
Standard
Brass
Number of Units Produced
66,000
26,400
9,900
Direct Materials Costs
$42,900
$26,400
$16,500
Direct Labor-Hours
450
450
600
Number of Orders
12
9
6
Number of Production Runs
3
3
6
Pounds of Material
16,500
6,600
3,300
Machine-Hours
638
140
80
Number of Inspections
3
3
3
Units Shipped
66,000
26,400
9,900
Actual labor costs were $15 per hour.
Complete the following:
Compute a predetermined overhead rate for year two for each cost driver using the estimated costs and estimated cost driver units prepared by the consultant. Also, compute a predetermined rate for year two using direct labor-hours as the allocation base.
Compute the production costs for each product for January using direct labor-hours as the allocation base and the predetermined rate computed in Part 1.
Compute the production costs for each product for January using the cost drivers recommended by the consultant and the predetermined rates computed in Part 1. (Note: Do not assume that total overhead applied to products in January will be the same for activity-based costing as it was for the labor-hour-based allocation.)
Management has seen your numbers and wants an explanation for the discrepancy between the product costs using direct labor-hours as the allocation base and the product costs using activity-based costing. Write a brief response to management.
Assessment 3 Part 3: Quality Improvement
Compute and explain the rationale for using or not using the proposed new material based on the associated costs. Give other factors that should also be taken into consideration for this decision. Show all calculations.
Part 3 Scenario
Bonded Fencing, Inc., produces metal gates in two processes: shaping, in which metal is bent to the correct shape, and fastening, in which the bent metal pieces are welded into gates. The shaping process has a capacity of 11,000 units per year; welding has a capacity of 15,400 units per year. Demand is high. At a sales price of $550 per unit, the company can sell whatever output it can produce.
Bonded can start only 11,000 units into production in the shaping department because of capacity constraints. 1,650 units are found to be defective in the shaping department annually. Defective units are not detected until the end of production, at which time they are scrapped. Unit costs in the shaping department, including good and defective units, equal $275 per unit, with an allocation of the total fixed manufacturing costs of $825,000 per year to units.
Bonded Fencing: Unit Cost
Item
Value
Direct Materials (variable)
$125
Direct Manufacturing, Setup, and Materials Handling Labor (variable)
$50
Depreciation, Rent, and Other Overhead (fixed)
$75
Total Unit Cost
$250
The fixed cost of $75 per unit is the allocation of total fixed costs of the shaping department to each unit, whether the units are good or defective.
The good units from the shaping department are sent to the fastening department. Variable manufacturing costs in the fastening department are $75 per unit and fixed manufacturing costs are $550,000 per year. There is no scrap in the fastening department. Therefore, the company’s total sales quantity equals the shaping department’s good output. The company incurs no other variable costs.
The company’s designers have discovered that, by using a new type of direct material, the company could reduce scrap in the shaping department from 1,650 units to 550 units. Using the new material would increase the direct materials costs to $180 per unit in the shaping department for all 11,000 units. Recall that only 11,000 units can be started each year.
Complete the following:
Should Bonded use the new material and improve quality? Assume that inspection and testing costs of $132,000 per year will be reduced by $22,000 with the new materials. Fixed costs in the shaping department will remain the same whether 8,500 or 9,500 units are produced.
What other nonfinancial and qualitative factors should Bonded management consider in making the decision?
Assessment 3 Part 4: Allocation Methods Comparison
Allocate the cost to the service department using all three methods: direct, step, and reciprocal, then comment on your findings in a paragraph. Show all calculations.
Part 4 Scenario
Liberty Company has two service departments: administration and accounting, and two operating departments: domestic and international. Administration costs are allocated on the basis of employees and accounting costs are allocated on the basis of number of transactions. A summary of Liberty operations follows:
Liberty Company: Summary of Operations
Administration
Accounting
Domestic
International
Employees
—
25
45
180
Transactions
27,500
—
22,000
88,000
Department Direct Costs
$396,000
$158,400
$1,029,600
$3,960,000
Complete the following:
Allocate the cost of the service departments to the operating departments using the direct method.
Allocate the cost of the service departments to the operating departments using the step method. Start with Administration.
Allocate the cost of the service departments to the operating departments using the reciprocal method.
Comment on the results.
Competencies Measured
By successfully completing this assessment, you will demonstrate your proficiency in the course competencies through the following assessment scoring guide criteria:
Competency 3: Use cost accounting concepts to operate job, process, and activity-based cost systems.
Prepare production cost report.
Determine predetermined overhead rate for each cost driver using the estimated costs and estimated cost driver units, and predetermined rate for using direct labor-hours as the allocation base.
Explain use of new material and quality improvement.
Allocate service department cost using direct, step, and reciprocal methods.
Competency 5: Communicate in a manner that is professional and consistent with expectations for professionals in the field of accounting.
-
cf_assessment3_template.xlsx
a month ago
05.09.2022
15
- Home
- Homework Answers
- Blog
- Archive
- Tags
- Reviews
- Contact
-
"96% of our customers have reported a 90% and above score. You might want to place an order with us."
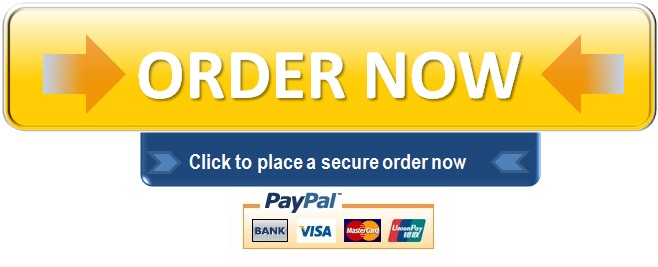