[ad_1]
Team Z 2
1. Issue Analysis:
KB Bakery owners Kelvin and Bridget are working long hours around 15hours from 7am to 10pm
in order to meet the demand for cakes even though they have one operator working from 7am to
4pm daily (8hours).
Kelvin believes that there are many un-explored opportunities which can be considered for to
improve productivity. Issues are analyzed below that can improve productivity of the bakery.
The owners are open to new ideas in terms of all possible avenues that can to speed up the
process and to improve its performance generally.
Here is our issue analysis which will be tested in our simulation model.
No. | Issue | Hypothesis | End Product |
1. | Does the increase in no. of cakes in a batch will increased productivity? Current no. of standard cakes in a batch is 10. |
Yes, it can reduce the waiting time and improve system efficiency and productivity |
The Bakery can finish the standard orders within time and can also do some additional bespoke order which will eventually improve sales. |
2. | Can we increase the capacity of the oven? |
Yes, it will reduce the processing time and improve the waiting period. |
Process can be more efficient and will improve productivity. |
3. | Can we analyze smart selection of decorator to send a batch of cakes for the shortest queue instead of random selection which is currently in practice? |
Yes, it will reduce waiting time for decoration. |
Decoration process will be more effective and productivity will improve |
4. | Can we use an additional resource in the shape of Kelvin and Bridget for some tasks to improve the processing time of each batch? |
Yes, additional resource in the shape of Kelvin and Bridget are already available during process, if some tasks are assigned to them that will free up the operator to prepare for next tasks. |
Overall process will improve and waiting time will be minimized, eventually productivity will improve. |
Team Z 3
2. Key Performance Indicators (KPI):
• Waiting (Queue) Time:
The total waiting time for a batch of standard or bespoke cake to start a process.
• Process Time (Total):
The total time to finish a process for one single batch of standard or bespoke cakes.
• Resource utilisation:
The rate of time that the resources are doing work.
• Process Time (Oven):
The total time to finish an oven process time for one single batch of standard or bespoke
cakes.
• Baking Process (Queue):
The total amount of time from the Pre-heating to cleaning for both bespoke and standard
cakes.
• SCARA Number In & Number Out:
The quantity of cakes (Bespoke and Standards) that are used in the decorator robots.
• Entities WIP:
Work in Progress for the operators, robots(SCARA) and Oven.
3. Arena Model:
O r d e r R e c e iv in g A s s ig n T im e I n t e r n a l_ O r d e r ? Or d e r _ Nu m b e r De c is io n _ M a k in g ? 0 |
P r e p a r a t io n Re c ip e c h B e _ S p o k e Or d e r R e c ip e P r e p a r a t io n 0 |
O r d e r N u m b e r 2
Va r ia b le s
v M T B F 1
v M T T R 1
v E x t e r n a lO r d e r
v O r d e r N u m 2
v O r d e r Nu m 2
U p d a t e
B a k in g , C le a n in g , D e c o r a t in g , P a k in g
Ne x t O r d e r
T r u e
F a ls e
S t a n d a r d B a t B e s p o k e O r d e r s
At t r ib u t e s
a T im e O u t
a O r d e r N u m
a T im e I n S y s t e m
a T im e I n
Qu e u e _ F o r _ Ne x t _ D a y
B a t c h _ Of _ 1 0
C o u n t e r _ Or d e r
I n t e r n a l V a r ia b le s
E x t e r n a l V a r ia b le s
Ne x t _ Or d e r
Ne w_ Or d e r
Va r ia b le s
v O r d e r
v I n t e r n a lO r d e r
0
aOr der Num
0
0
TNOW
08:00:00
vExt er na l Or der
0
T AVG(B aki ng P rocess. Queue. W ai tingT i me)
0
E nti ti esW IP (Order R ecei ve)
0
DAVG(rOperat or. NumberB usy)
0.00
INAC TIVE_R ES
0
T AVG(Nex t Day Ord er
0
T AVG(S C AR A1. Queue. W ai ti ngT i me)
0
T AVG(S C ARA2 . Qu eu
0
0
FAILED_R ES
0
S CARA1 .Nu mb erOu t
0
S CARA1 .Nu mb erIn
0
S CARA2 . Nu mb erIn
0
S CARA2 .Nu mb erOu t
0
B aking Process. NumberOut
0
Team Z
Sub Model 1:
Sub Model 2:
Ba k in g Pr o c e s s
O v e n Co o lin g
O v e n Cle a n in g
O r d e r o t o : Ne x |
G | T o t a l B e s p o k e |
Cle a n in g De c o r a t o r |
||
0 |
De c o r a t io n Se le c t io n
T r u e
F a ls e Ro b o t _ 2 0 |
P a c k in g _ B e s p o 0 |
k e n |
SCARA2 | Be s p o k e a r t o n St y le |
C |
SCARA1 | O p e r a t io n s Pa c k in g |
Ro b o t _ 1 | P a c k in g _ S t a n d a r d s |
1 0 m in De la y f o r c o o lin g
Pr o c e s s UNI F ( 5 , 1 0 ) f o r C le a n in g
O v e n Se t u p
3 5 m in De la y f o r B a k in g
UNI F ( 8 , 1 2 ) f o r P r e h e a t
De c is io n f o r I c in g a n d C o v e r t u r e
UNI F ( 1 5 , 2 0 ) f o r C le a n in g
On c e _ Or d e r _ I s _ c o m p le t e _ m o v e _ t o Ne x t _ Or d e r
St an d a r d _ f in is he d
Cu s t o m iz e d _ Fin is h e d
T o t a l S t a n d a r d s
0
0
0
0
0
0
0
0
T r u e
F a ls e Queue_For_Next _Day |
Next Day O r der |
Bespoke models
Ext er nal O r der
vExt er nalO r der 2
Updat e
Cust om ize_Order
Count er_Ext ernalOrder
0 Be_SpokeOrder
0
4. Model Design Specifications:
The Model design specifications like resource arrays, process time and failure/repair time
can be seen below:
Resource Array
No. | Resource Name | Capacity |
1 | Operator 1(Monday to Friday) | 1 |
2 | Operator 2 (Saturday to Sunday) | 1 |
3 | Oven | 1 |
4 | SCARA decorator 1 | 1 |
5 | SCARA decorator 2 | 1 |
Process Time Array
Process Name | Expression | Time (Min) | ||
Assemble and mix required ingredients |
TRIA(10,15,20) | 10 | 15 | 20 |
Oven Preheat (Same time as Assemble) |
TRIA(10,15,20) | 10 | 15 | 20 |
Fill Cake with required mixture | UNIF(8,12) | 8 | 12 | |
Baking | CONSTANT | 35 | ||
Cooling | CONSTANT | 10 | ||
Clean | UNIF(5,10) | 5 | 10 | |
Standard Cakes (Catering) | CONSTANT | 8 | ||
Bespoke Cakes (Customized) | UNIF(8,12) | 8 | 12 | |
Bespoke Cakes (Wedding) | UNIF(15,25) | 15 | 25 | |
Carton Style on the Packer | CONSTANT | 5 | ||
Packing Operation | EXPO(0.5) | 0.5 | ||
Decorators Cleaning | UNIF(15,20) | 15 | 20 | |
Customized cakes | EXPO(5) | 5 | ||
Customized Cakes Average order | DISC(0.6,1,0.9,2,1.0,3) |
Team Z 7
Probability of Failure
Item Name | Expression | Time (Min) |
Decorator Jamming & Clogging | EXPO(160) |
Repair Time
Item | Expression | Time (Min) | |
Decorator Jamming & Clogging/Repair (Hours) |
EXPO(2) | 120 | |
Fresh Icing and Couverture mixture | UNIF(10,15) | 10 | 15 |
Team Z 8
5. Reports Output:
Queue:
Team Z 9
Processes:
Team Z 10
Resources:
Team Z 11
6. Results and Verification of the model:
Following data were derived from Arena Output Analyzer.
Time in Queue:
Following is the result for 30 Replications for 12-hour average shift.
Conclusion:
The above graph shows that the average time in queue is 0.000485 hour.
Team Z 12
Oven Utilization:
Conclusion:
Above graph shows that the average oven utilization is around 0.367 hour.
Team Z 13
Resource Utilization:
Conclusion:
This graph shows that the average resource utilization for operator 1 and 2 are around 0.292
hours
Team Z 14
Total Process Time:
Conclusion:
The graph above shows that the average time for 30 replications is around 0.27 hour.
Team Z 15
7. Statistical Data:
Across Replication Data (30 Replications) – Length of one replication = 12 hours /day shift
Data | Type | N | Sample Std. Dev. |
Time In Queue | Observation-based | 50 | 0.000843 |
Oven Utilization | Time based average | 1 | 0.49 |
Resource Utilization | Time-based average | 1 | 0.157 |
Total Process Time | Time-based average | – | 0.163 |
8. Conclusion
The above model for the KB bakery process was tested for the total number of orders in the
system and the number of output was confirmed to the total of both internal and external orders.
(it matches). We considered processing the cakes with a batch of 10 cakes coming into the
system. Therefore, we have around 7 to 9 total orders which comprise both internal and external
order. The 2 x external orders are programmed to be time based and goes to hold for next day
processing per day.
Based on the conditions of KB bakery we are able to replicate 50 standards order and 3 customize
orders per day. 80% of the standards orders are vanilla and 20% are chocolate. The system has
two sub models. The first one for the bespoke order and the second one for the bake process
itself.
The above model needs little bit of tweaking to be used for our issue analysis and to run and
comparative data.
[Button id=”1″]
[ad_2]
Source link
"96% of our customers have reported a 90% and above score. You might want to place an order with us."
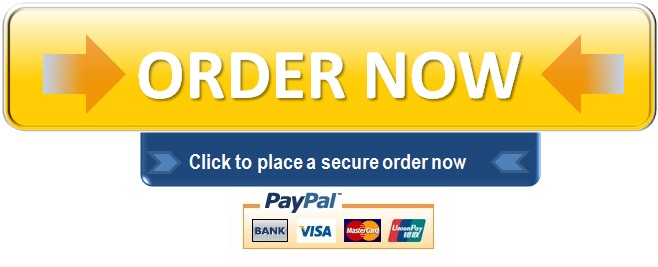